Um im ewigen Konkurrenzkampf der Unternehmen in der Wirtschaft mitzuhalten, reicht es nicht, auf dem gleichen Standard zu bleiben – Innovation und Entwicklung sind notwendig. Nur die Mitarbeiter, die sich stetig weiterentwickeln, schaffen es sich nicht nur über Wasser zu halten, sondern sogar an die Spitze der Hierarchie zu klettern.
Das Problem ist, dass Unternehmen genau wie auch Mitarbeiter veränderungsresistent sind. Es gibt innovativ entwickelte Prozesse und Konzepte, die Organisationen anwenden können, um eine kontinuierliche Verbesserung sicherzustellen.
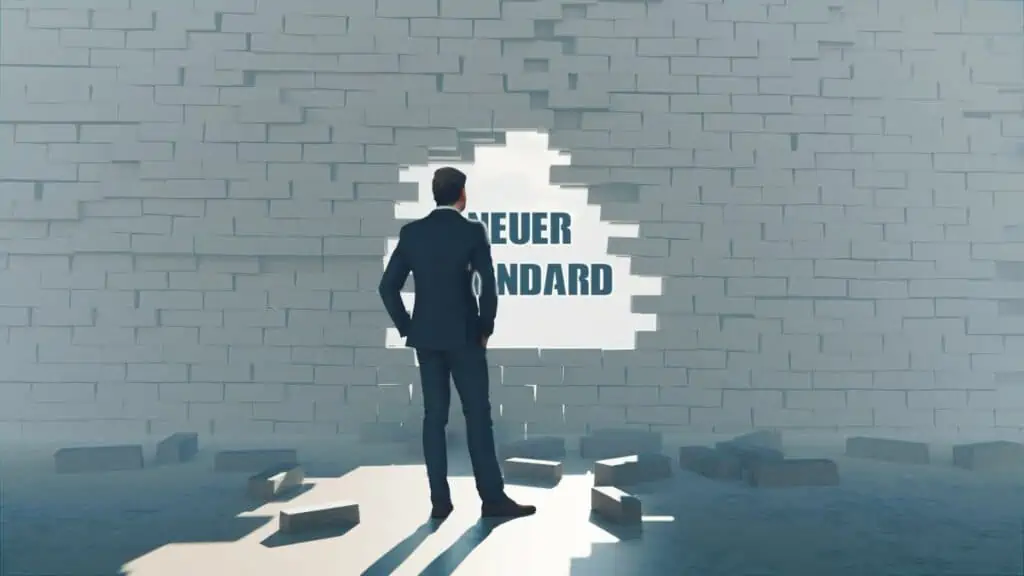
Die grundlegende Idee ist in der Industrie als Kontinuierlicher Verbesserungsprozess bekannt. Getauft wurde der kontinuierliche Verbesserungsprozess von W. Edwards Deming, welcher auch für den Deming-Kreis bekannt ist, die bekannteste Methode des KVP. Eine andere Bezeichnung dafür ist der PDCA-Zyklus, benannt nach den vier Phasen „Plan, Do, Check, Act“. Die Umsetzung dieser Schritte sollte immer wieder zyklisch wiederholt werden, um in Zukunft kontinuierliche Verbesserung zu erzielen.
Die Phasen des PDCA-Zyklus
PDCA-Zyklus Schritt 1: Plan Phase
Angefangen wird dieser Prozess standardmäßig in der Planungsphase, in der ein Aktionsplan erstellt wird. Es wird entschieden, wie der zukünftige Soll-Zustand aussehen soll und wie man am besten dorthin kommt. Das beinhaltet die möglichen Maßnahmen, die ausgeführt werden können, die zeitliche und finanzielle Realisierbarkeit und die nötigen Beteiligten. Am wichtigsten ist jedoch zuerst klar zu dokumentieren, was der Ist-Stand ist und diesen einzufrieren, dass man am Ende auch ganz sicher sein kann, was sich überhaupt verändert hat.
PDCA-Zyklus Schritt 2: Do Phase
Weiter in der Do Phase werden die Verbesserungsmaßnahmen ausgeführt und deren Durchführung observiert. Währenddessen wird geprüft, ob sich der Fortschritt in erwarteter Geschwindigkeit auf die Verbesserungsziele hinzu bewegt, oder eben nicht. Daran angeknüpft ist es auch wichtig zu überprüfen ob alle nötigen Ressourcen verfügbar sind und Deadlines eingehalten werden können.
PDCA-Zyklus Schritt 3: Check Phase
In der Check-Phase werden Ergebnisse gemessen und entschieden, ob die geplanten Ziele nach den im ersten Schritt ausgelegten Erfolgsfaktoren erreicht wurden oder nicht.
PDCA-Zyklus Schritt 4: Act Phase
Wenn das der Fall ist, dann wird als letzter Schritt in der Act-Phase entschieden, ob der neue Stand ab sofort als Standard genutzt werden soll. Hierbei wird der ausgearbeitete Verbesserungsvorschlag dem Verantwortlichen für das Produktionssystem übergeben und es wird entschieden, wie dieser in das aktuelle System aufgenommen werden kann. Oft ist es auch üblich einen Best-Practice-Katalog zu verwenden, der allen Mitarbeitern frei zur Verfügung gestellt wird. Wenn sich herausstellt, dass Ziele nicht erreicht wurden oder die Verbesserungen nicht nachhaltig aufgenommen werden können, werden aufgetretene Probleme analysiert und als Ziele für den nächsten Zyklus genommen.
Standardmäßig wird dieser Hauptprozess nicht vom gesamten Unternehmen verfolgt, sondern in abgetrennten Teams durchgeführt, die entweder nach Organisationseinheiten oder nach Prozessschritten gebildet und über einen Gruppensprecher moderiert werden.
Auch wichtig zu erwähnen: Falls die Ausgangszustände am Anfang der Nutzung des PDCA-Zyklus nicht ausreichend dokumentiert sind, dann wird der Prozess erstmal mit einer ausführlichen Analyse des Ist-Zustandes angefangen und danach beginnt der eigentliche Zyklus mit der Check-Phase statt der Plan-Phase. Ansonsten wäre es nicht möglich, sicher zu erkennen, dass man am Ende des Prozesses auch wirklich Verbesserungen erzielt hat. Die klaren Standards helfen außerdem dabei zu vermeiden, nur eine Veränderung anzusteuern, die vielleicht gar keine Verbesserung ist.
KAIZEN
Wenn man sich mit dem kontinuierlichen Verbesserungsprozess beschäftigt, kommt man am Begriff KAIZEN heutzutage nicht mehr vorbei. Vor allem wenn man die Entwicklung des Unternehmens wirklich ernst nimmt, ist es von größter Wichtigkeit, sich ausführlich mit dem Thema zu beschäftigen. KAIZEN steht für KAI = Veränderung und ZEN = zum Besseren, weshalb der Begriff oft synonym mit dem KVP verwendet wird, da sich die Prinzipien sehr ähneln.
Beide beruhen darauf, nicht durch Innovation, sondern durch stetige Optimierung des schon Existierenden eine dauerhafte Verbesserung zu fördern, was auf die Dauer oft größere Erfolge erzielt als eine Innovation. Außerdem liegt der Fokus beider nicht in erster Linie auf schnellem finanziellem Gewinn, sondern der Verbesserung der Produkte und Prozesse des Unternehmens, was auf lange Sicht gewinnoptimierend ist.
Der Hauptunterschied besteht tatsächlich in den damit verbundenen kulturellen Unterschieden. KAIZEN ist nämlich um einiges mehr als nur ein Handlungsprinzip. Es beschreibt eine übergreifende japanische Philosophie, die in den Unternehmen und im privaten Leben der Japaner Anwendung findet. Hier werden kleine, undramatische Schritte über einen langen Zeitraum gegangen. Im Vordergrund des Ganzen stehen die Menschen und es wird jeder in den Prozess involviert, während gerne an Konventionen und bestehenden Abläufen festgehalten wird. Das Ganze zielt darauf ab, sich langsam, aber sicher weiterzuentwickeln.
Das liegt theoretisch auch dem kontinuierlichen Verbesserungsprozess zugrunde, der allgemein eher den Verbesserungsprozess in westlichen Unternehmen beschreibt. Durch die großen kulturellen Unterschiede wird es jedoch im Westen nicht immer so angewandt. Hier ist nämlich die Herangehensweise meistens auf große dramatische Veränderung konzentriert, in der existierende Abläufe komplett neu aufgebaut werden. Außerdem liegen hier meist eher Technologie und bestimmte Individuen im Vordergrund, statt allen Mitarbeitern. Dennoch ist KAIZEN auch in westlichen Firmen eine der Standardmethoden zur Unterstützung von kontinuierlichen Verbesserungsprozessen.
KAIZEN steht hierbei einer Innovation nicht komplett gegenüber, sondern die beiden Konzepte arbeiten oft Hand in Hand. KAIZEN wird immer so lange genutzt, bis der existierende Standard nicht mehr ohne große Veränderung verbessert werden kann. Dann wird eine Innovation herbeigeführt, welche oft mit hohem finanziellem Aufwand verbunden ist, aber auch drastisch große Verbesserungen bewirkt.
Innovationsmanagement
Der Begriff Innovation beschreibt nicht nur den Prozess der Gewinnoptimierung, sondern konzentriert sich auf die Optimierung der einzelnen Abläufe jedes einzelnen Mitarbeiters. In der Zukunft profitiert jeder Angestellte von den Verbesserungen, und zwar nicht nur durch den Genuss eines besseren Arbeitsablaufs. Während beim kontinuierlichen Verbesserungsprozess die Hauptanalysearbeit von ausgewählten Teams gemacht wird, sollte trotzdem die gesamte Firma über den KVP geschult werden und seine Verbesserungsvorschläge miteinbringen. Dadurch fühlen sich Mitarbeiter gehört und das Unternehmen profitiert von mehr motivierten Arbeitskräften.
Dem folgend bleiben Angestellte auch eher beim Unternehmen, als wenn sie von immer gleichbleibenden Problemen im Arbeitsablauf frustriert werden. Das spart sowohl Zeit als auch Geld für die Rekrutierung und Einarbeitung neuer Mitarbeiter.
Durch die Analyse und immer weiterverbesserte Ressourcennutzung wird Stück für Stück die Verschwendung bei der Produktion reduziert, was nicht nur viel Geld spart, sondern auch allgemein nachhaltiger ist. Vor allem in der Ingenieurstechnik wichtig ist auch der Aspekt der Fehlervermeidung. So können nicht nur Ergebnisse beschleunigt, sondern auch Unfälle vermieden werden, was das Unternehmen gleichzeitig sicherer und beliebter macht. Eine geeignete Methode hier ist die Fehler-Ursachen-Analyse.
Wenn sich Unternehmen mithilfe des kontinuierlichen Verbesserungsprozesses optimieren, dann bedeutet das auch, dass sie immer an der Spitze der Forschung beteiligt sind. So werden neueste Technologien zum Einsatz gebracht, um maximale Effizienz zu erzielen und mit der Konkurrenz mithalten zu können.
Auch nicht zu unterschätzen ist der Aspekt der Digitalisierung, welcher durch KVP effizient eingeführt und verbessert werden kann. Das hat zur Folge, dass alte analoge Prozesse durch die digitale Überholung bei weitem in ihrer Geschwindigkeit übertroffen werden.
Fazit
Während es sich hier schon um handfeste Prinzipien und Methoden handelt, ist die Anwendung allerdings dennoch individuell anpassbar und jedes Führungsteam bzw. Management muss selbst herausfinden, wie genau es den KVP am besten gestaltet. Oder in anderen Worten: Jedes Unternehmen muss den KVP erst für sich selbst optimieren, bevor der KVP das Unternehmen optimieren kann. So oder ist es für jedes Unternehmen empfehlenswert, den KVP für sich zu nutzen, um im Konkurrenzkampf nach außen mithalten zu können und eine Reihe von Vorteilen in der Wirtschaft nicht zu verpassen.
Kein Problem, einfach für unsere Blog-News anmelden!