Das Thema Regalplanung ist ein weites Feld. Es sollten bei der Planung stets die individuellen Anforderungen zur Findung einer effizienten Lösung betrachtet werden. Gerade in der heutigen Zeit in der Pandemien, politische Konflikte und Engpässe in der Versorgung immer deutlicher auch die Schwachstellen der Lieferketten aufzeigen, spielt eine ausgeglichene und flexible Lagerung von Rohstoffen, Halbzeugen und Produkten eine immer wichtigere Rolle.
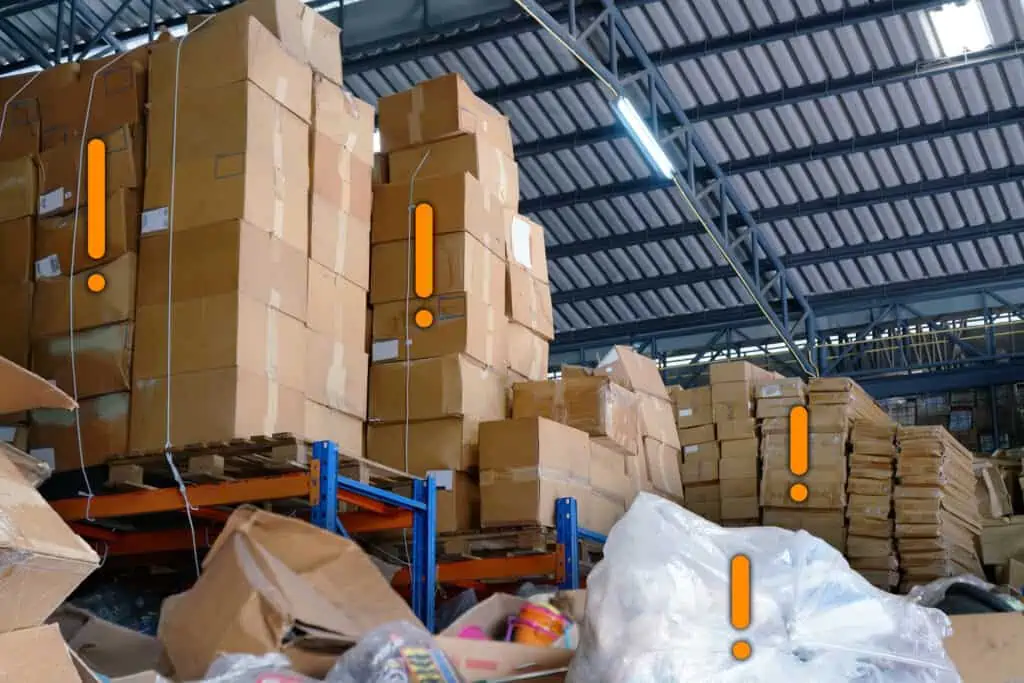
Die Lieferzeit als bestimmender Faktor
Denn neben der prinzipiellen Lieferbereitschaft gewinnt die Lieferzeit bei den Kunden mehr und mehr an Bedeutung. Ein Trend den jeder gerade an Verkehrsknotenpunkten, Haupttransportwegen oder auch in der Nähe von großen Städten in Form von Logistikzentren, die wie Pilze aus dem Boden schießen, sicherlich schon wahrgenommen hat.
Die folgende Aussage macht es in Zahlen noch etwas deutlicher. Im Jahr 2021 überschritt in Deutschland der Bedarf an Lagerflächen erstmalig die 8 Mio. m² Marke, womit der Wert vom Vorjahr um 25% übertroffen wurde (Quelle: Logistik-und-Industriemarktueberblick-JLL-Deutschland.pdf). Warum also Lagerflächen notwendig sind, welche Rolle hierbei Regale spielen und was es dabei zu beachten gilt, soll in den folgenden vier Punkten aufgezeigt werden.
1. Warum sind Lager notwendig?
Die Antworten hierauf können sehr unterschiedlich sein und manch einer kann gleich mehrere Gründe aufführen. Aus meiner Sicht können die Gründe auf die folgenden drei wesentlichen Kategorien aufgeteilt werden:
- Technologisch bedingte Lagerung
Bei dieser Lagerung geht es darum, dass Teile nach einem Prozess warten müssen, um einen gewissen Zustand zu erreichen. Beispiele hierfür sind Teile aus der Wärmebehandlung, die vor der Weiterverarbeitung abkühlen müssen oder bei der Produktion von Käse, der reifen muss.
- Prozessbedingte Lagerung
Hier dient die Lagerung dem Ausgleich unterschiedlicher Prozesszeiten. So arbeitet beispielsweise die Fertigung dreischichtig, um die benötigten Teile für die Montage eines Produktes herzustellen. Für die Montage reicht es jedoch zweischichtig zu arbeiten, um die gefertigten Teile zu montieren. Somit bedarf es eines gewissen Pufferlagers zwischen der Fertigung und Montage, da die Teile in der dritten Schicht nicht direkt weiterverarbeitet werden können.
- Organisatorisch bedingte Lagerung
Bei dieser Art Lagerung spricht man auch von einer Vorratslagerung. Das eigentliche Ziel ist hier, Produkte schnell verfügbar zu haben. Das bedeutet, wenn etwas benötigt wird, kann es sofort dem Lager entnommen werden und muss nicht erst produzieren werden.
Kürzere Lieferzeit vs. Kosten
Insbesondere die organisatorisch bedingte Lagerung ist der wesentliche Treiber für die eingangs erwähnte starke Zunahme an benötigten Lagerflächen. Die dadurch erreichbare höhere Verfügbarkeit und kürzere Lieferzeit der Produkte steht jedoch im Widerspruch zu den damit verbundenen hohen Beständen, den hohen Kapitalbindungskosten und auch dem Risiko auf den Produkten sitzen zu bleiben. Wichtig ist an dieser Stelle, die Chancen und Risiken abzuwägen und sich für eine flexible Lösung zu entscheiden. Je besser man hierbei den Bedarf bei den Kunden über die Zeit abschätzen kann, um so besser kann man planen.
Oft spielen hier auch die eigenen Lieferanten eine wichtige Rolle. Gibt es mehrere Lieferanten für entsprechende Teile und können diese auch kurzfristig liefern, da sie in der Nähe angesiedelt sind, braucht man keine große Bevorratung. Gibt es nur einen Lieferanten am anderen Ende der Welt, ist die Abhängigkeit sehr groß und man sollte definitiv genügend Vorrat haben, um bei einem Engpass noch genug Zeit zum Finden von Alternativen zu haben. Dies sind jedoch häufig Themen, die durch Experten im Management getroffen werden und nur im bedingten Maß durch die Lagerplanung zu beeinflussen sind.
2. Welche Lagerart eignet sich?
Ist der Grund der Lagerung definiert, ergeben sich im nächsten Schritt automatisch die Eingangsinformationen für den Planer, um die geeignete Lagerart zu bestimmen. Zu diesen Informationen gehören im Wesentlichen folgende:
- Anzahl
Die Anzahl gibt an, welche Menge an Teilen bzw. Produkten gelagert werden soll.
- Art
Die Art beschreibt, um welche Teile bzw. Produkte es sich handelt und gibt Aufschluss über Lagerbedingungen. So kann z.B. in Stückgüter, Schüttgüter, Gefahrgut, empfindliche Güter oder auch Flüssigkeiten unterschieden werden. Hieraus kann auch abgeleitet werden, ob gekühlt gelagert werden muss oder man ein Außenlager verwenden kann.
- Größe und Form
Die Größe und Form spielt insbesondere dann eine Rolle, wenn keine Verpackungen oder Transporthilfsmittel, wie Paletten oder Boxen, genutzt werden. Ansonsten ist die Packgröße das entscheidende Maß zur Lagerung.
- Gewicht
Das Gewicht hat Einfluss auf die Festlegung der Packgröße (bei Nutzung von Verpackungen oder Transporthilfsmitteln) und damit dann auch wie gelagert werden kann. Dies betrifft Aspekte, wie z.B. Stapelbarkeit, Bodenlasten und Regalarten.
- Packgröße
Die Packgröße orientiert sich meist an der Transportlosgröße. So wie die Teile bzw. Produkte transportiert werden, werden sie häufig auch gelagert. Genutzte Angaben sind hier z.B. Teile pro Behälter oder auch Behälter pro Palette. Die Packgröße definiert sich dann über den Behälter oder auch die Palette.
Da es sich bei sehr vielen Teilen bzw. Produkten um Stückgüter handelt, erfolgt in der Regel die Lagerung in Blöcken oder Regalen. Bei einem Blocklager ist der technische Aufwand am geringsten. Es wird lediglich eine Fläche benötigt. Die Effizienz hängt jedoch stark von der Stapelbarkeit und der Varianz der zu lagernden Produkte ab. Ganz grob kann man sagen, je höher man stapeln kann und je geringer die Varianz der Produkte ist, desto besser eignet sich ein Blocklager.
In vielen Fällen die beste Wahl – Regale
Die maximale Flexibilität hat man jedoch bei der Lagerung in Regalen. Um die Flächen ideal auch in der Höhe zu nutzen, bedient man sich verschiedener Regalsysteme. Je nach einzulagerndem Produkt kommen hier Hochregale, Palettenregale, Kragarmregale, automatische Regalsysteme oder auch individuelle Regale mit entsprechender Lagertechnik zum Einsatz. Dem Regalplaner bieten sich hier von verschiedensten Herstellern eine ganze Reihe an Katalogen mit Angeboten verschiedenster Technik aus denen er nur noch auswählen muss. Bei einem solch großen Sortiment ist man als Regalplaner gut beraten, auch die im folgenden Punkt beschriebenen Aspekte im Projekt zu berücksichtigen.
3. Was gilt es noch bei der Regalplanung zu beachten?
Neben den harten Faktoren von der Anzahl bis zur Packgröße spielen auch die mehr oder weniger weichen Faktoren eine nicht zu vernachlässigende Rolle bei der Auswahl des richtigen Regalsystems. Folgende Faktoren erachte ich an dieser Stelle für wichtig:
- Zugriffsdauer
Hier versteht man, wie lange für einen Ein- und/oder Auslagerungsprozess benötigt wird. Insbesondere bei Automatiklagern ist dies neben der Umschlagleistung eine wichtige Kenngröße. Aber auch bei nicht automatisierten Lagern spielt dies eine wichtige Rolle, da hier oft gesucht werden muss. Die Ursache liegt meist an der Übersichtlichkeit.
- Übersichtlichkeit
Die Übersichtlichkeit ist definitiv ein Maß für die Ordnung im Lager und wirkt sich bei nicht automatisierten Lagern direkt auf die Zugriffsdauer aus. Denn je übersichtlicher die Regale sind, umso schneller findet man das gesuchte Material und kann es dem nächsten Prozess bereitstellen. Nicht selten werden hierfür auch zur Information Planogramme erstellt.
- Sicherheit
Bei der Regalplanung sollte im Unternehmen die Sicherheit immer an oberster Stelle stehen. Es gilt, Unfälle z.B. durch abstürzende Teile oder auch Kollisionen mit Staplern zu vermeiden. Dies beginnt schon mit der Planung die passende Auslegung der Regale, geht über geeignete Belegung (schwere Sachen unten, leichte Sachen oben) bis hin zu individuellen Einweisungen der Werker.
- Sauberkeit
Die Sauberkeit sollte immer gewährleistet sein und ist eine Grundvoraussetzung für die Sicherheit, die Qualität der Waren und den Erhalt der Technik.
- Flexibilität
Die Flexibilität gibt an, wie einfach und schnell das geplante Regalsystem an Veränderungen bezüglich Menge und Varianz angepasst werden kann. Gerade automatische Systme sind meist auf ein definiertes Warenspektrum optimiert und lassen sich meist nur mit erhöhtem Aufwand anzupassen. Beim Planen sollte also hier auch schon an die Zukunft gedacht werden.
Lagertechnik automatisiert, aber flexibel
Da der Trend in der Produktion zu autonom fahrenden Transportmitteln (FTS) geht, führt dies natürlich auch zu einer Automation bei der mobilen und stationären Lagertechnik. Zudem findet auch bei der Software zur Steuerung der automatischen Systeme Schritt für Schritt eine immer weitere Vereinfachung statt. Das soll nicht heißen, dass in Zukunft alles automatisch läuft aber einige der beschriebenen weichen Faktoren (Zugriffsdauer, Übersichtlichkeit, Sicherheit etc.) erfüllen sich damit von selbst. Ein gutes Beispiel, um die Vorteile aus beiden Welten (automatisch/speziell und manuell/flexibel) miteinander zu verbinden, ist die online Navigation der Werker zu den Regalstellplätzen über „Pick by light“.
4. Welche Regalanordnung und Regalbelegung?
Egal ob die Regale automatisch oder manuell belegt werden, ein Thema bleibt, und zwar das der kurzen Wege. Denn je länger die Wege der Transporte sind, um so mehr braucht man an Ressourcen und um so länger dauert es, die Ware am richtigen Ort bereit zu stellen. Bei automatischen Lagern wird dieses Thema bei der Belegung der Regalfächer durch Algorithmen bereits optimiert und auch ausgewertet. Bei manuellen Lagern ist die Situation oft diffus und nicht selten wird dort gelagert wo Platz ist.
Eine Möglichkeit, die Belegung der Stellplätze zu planen, besteht darin, die Regale zu zonieren. In der A-Zone werden alle Produkte gelagert, die eine hohe Umschlagshäufigkeit haben, bzw. auf die oft zugefriffen wird. Die Anordnung dieser Zone sollte im Layout auch die kürzesten Wege erhalten. Im folgenden Bild wird das Prinzip dargestellt.
Eine weitere Möglichkeit besteht darin, die Stellplätze im Regal so zu belegen, dass im unteren Bereich, der einfach zugänglich ist, die Produkte mit einer hohen Umschlagshäufigkeit liegen. Die oberen Regalplätze nutzt man für die Produkte, auf die seltener zugegriffen wird. Dies wirkt sich neben der Effizienz auch positiv auf die Sicherheit aus. Durch Erstellen von Planogrammen für die einzelnen Regale erhöht man zudem die Transparenz der Belegung und hat die Wege optimal gestaltet.
Zur Regalplanung und auch zum Erstellen entsprechender Layouts bietet sich natürlich die Nutzung einer Software an.
Weiterführende Artikel zum Thema:
- Wie funktioniert die Flächenplanung in der Produktion?
- Wie Materialflussplanung hilft Logistik, Produktion und Lager zu optimieren
- Flächendimensionierung in der Fabrikplanung
- Was Osternester mit Palettenregalen verbindet
Kein Problem, einfach für unsere Blog-News anmelden!