The subject of warehouse planning is a very broad one. Warehousing plays a crucial role in streamlining a company’s supply chain. When planning is done, individual requirements should always be taken into account in the search for an efficient warehouse layout design. Especially in the current times of pandemic, political conflicts and supply bottlenecks, with the weak links in supply chains being revealed all the more evidently, a balanced and flexible approach to the storage of materials, work in progress and finished products play an increasingly important role. How do I determine if I need pallet racking in certain storage areas of my warehouse layout or if perhaps a block storage system is more suitable?
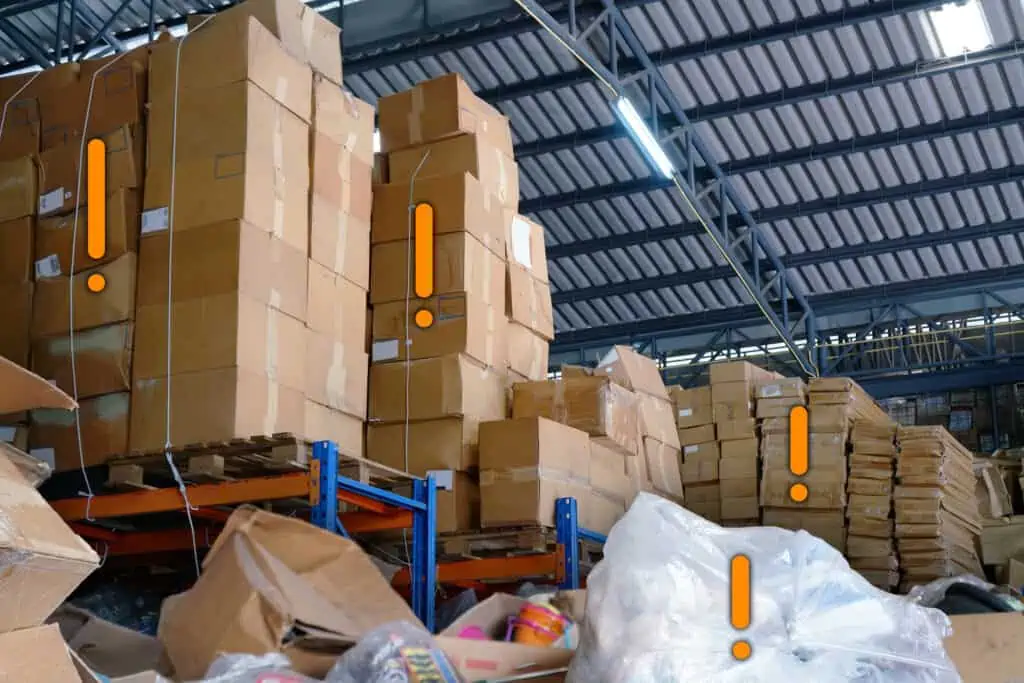
Delivery times as the determining factor
In addition to the general ability to supply, specific delivery times are gaining importance for more and more customers. A trend which is clear for all to see from the logistics centers which are springing up like mushrooms at major traffic interchanges, along main transport routes and on the outskirts of larger towns and cities.
The following statement confirms the impression with two striking figures. In 2021, the demand for logistics space in Germany exceeded 8 million m² for the first time, and thereby represented an increase of 25% compared to the previous year (source: Logistik-und-Industriemarktueberblick-JLL-Deutschland.pdf). The following four points are intended to shed light on why so much storage space is necessary, the role played by industrial rack systems, and what must be taken into account when addressing the issue.
1. Why is storage necessary?
The possible answers to this question are extremely diverse, and many a planner will be able to list several reasons. In my opinion, the various explanations can be classified into the following three basic categories:
- Technologically necessary storage
This type of storage applies where waiting times must be observed after a process to allow the parts or products concerned to reach a certain state. Examples here are parts which have undergone heat treatment and must be allowed to cool before further processing, or the production of cheese which must be given time to mature.
- Process-related storage
In this case, storage serves to compensate differences in process times. For example: A production department works three shifts to manufacture the parts for a product. In the assembly department, on the other hand, it only takes two shifts to assemble those parts. This necessitates a buffer store between manufacturing and assembly, as the parts from the third shift cannot be used immediately.
- Organizationally necessary storage
This type of storage could also be called stock storage. The objective here is to ensure that the products are available at short notice. This means that, when a product is requested, it can be taken straight from the warehouse and does not need to be manufactured first.
Shorter delivery times vs. costs
It is organizationally necessary storage, in particular, which is driving the aforementioned increases in the demand for logistics warehouse space. The improved product availability and shorter delivery times, however, conflict with the correspondingly higher stock levels, high capital commitment costs, and also the risk of not actually being able to sell the products. It is thus important to weigh up the risks and benefits and to choose a flexible solution. The better you are able to estimate customer demand over time, the better the planning outcome will be.
A company’s own sub-suppliers may also play an important role in the considerations. If there are several suppliers for a particular part and they are all able to deliver at relatively short notice because they are located close by, then there is no need to maintain large stocks. If your only supplier is located on the other side of the world, however, the dependence is much greater and you should definitely ensure that you have sufficient parts in stock, so that enough time remains to seek an alternative in case of a bottleneck. But these are frequently decisions that are taken by management experts and can only be influenced to a minor extent in warehouse planning.
2. Which type of storage is suitable?
Once the reason for storage has been defined, this automatically provides the planner with a set of essential parameters for subsequent determination of the most suitable type of storage and industrial racking in a warehouse layout. Such parameters include:
- Quantities
The quantities of the parts or products which are to be stored. This determines, among other things, the capacity and thus size of racking systems, for example, for a pallet rack.
- Type
Information on which parts or products must be stored and any particular storage conditions which may apply. This permits distinctions to be made between piece goods, bulk materials, hazardous goods, sensitive goods or liquid products, for example. It is also possible to derive whether refrigerated storage is necessary, or whether an outdoor storage area can be used.
- Size and form
The size and form are especially relevant where it is not possible to use packaging or transport aids such as pallets or boxes. Otherwise, the packing unit is the decisive dimensional parameter for storage.
- Weight
The weight influences the specification of a packing unit (where packaging or transport aids are used) and thus also how the parts or products can be stored. Associated aspects are stackability, floor loads and rack type, among others. For example, this then applies to the design of a steel beam of a pallet rack, whether it can bear 2 tons or up to 4 tons.
- Packing unit
The packing unit is commonly dependent on the transport batch size. Parts and products are often stored in the manner in which they are transported. Examples of the specifications used here are the number of parts per container or the number of containers per pallet. The packing unit is thus defined by way of the container used and/or the associated pallets. That is why flexible pallet racking systems are often used in warehouse design.
As many, if not most parts or products are handled as piece goods, their storage is generally organized in blocks or racks. The technical expenditure is lowest for block storage. Suitable warehouse space is all that is needed. The efficiency, however, is highly dependent on the stackability and the variance of the products to be stored. Generally speaking, the higher the products can be stacked and the lower their variance, the more suitable block storage becomes.
In many cases the best choice: Rack storage
Maximum flexibility, however, is achieved with rack-based storage in a warehouse layout. Various rack systems are used to make optimum use of the occupied warehouse space, also in terms of height. Depending on the product to be stored, the planner can choose between high-rise racks, pallet racks, cantilever racks, automatic rack systems or even custom-designed racking with corresponding handling equipment. The preferred solution is found simply by browsing a sheer endless range of different offers in the catalogs of the most varied shelving or racking manufacturers. But where so many different variants are available, the planner is well advised to give due consideration to the following aspects when creating a warehouse layout design.
3. What else must be taken into account when creating rack storage in a warehouse layout?
In addition to hard factors ranging from quantities to packaging unit, there are also a number of essentially soft factors which also play a far from negligible role in selection of appropriate racking in a warehouse layout. The following are factors which I consider to be important in this context:
- Access time
This refers to the time required to complete the process of taking a product into or out of storage. That includes loading and unloading, storage and retrieval plus transportation time. Especially in automatic warehouses, this is an important parameter alongside the transshipping performance. But it also has a significant role to play in non-automated warehouse operations, where frequent searching may be necessary. The reasons usually lie in a lack of structural clarity in warehouse layout design.
- Structural clarity
Structural clarity is a definitive measure for the tidy organization of a warehouse and has direct influence on the access time in non-automated warehouses. The clearer the organization of the racks, the faster the desired materials can be found and made available to the next process. It is here also commonplace to use planograms for information.
- Safety
When planning rack storage in the company, safety should always be given top priority. It is crucial to avoid accidents, e.g. injuries due to falling parts or collisions with forklift trucks. This begins with suitable dimensioning of the rack systems in planning, continues via appropriate shelf assignments (heavy items at the bottom, light items at the top) and extends to individual instructions for the workers and clearly visible floor markings already in the warehouse layout.
- Cleanliness
Cleanliness should always be guaranteed, as a basic prerequisite for safety, the sustained quality of the goods and proper functioning of the equipment in warehouse operations. This also includes lean methods, as briefly touched on below.
- Flexibility
Flexibility of a warehouse design refers to how quickly and simply the planned industrial racking can be adapted to changes in product quantities and variance. Automatic systems, in particular, are usually optimized for a defined spectrum of goods and can only be adapted with considerable outlay. Planning should thus also take into account expectations for future development.
Automated warehouse systems can also be flexible
The trend towards autonomous, automated guided vehicles (AGV) in production environments is naturally leading to the automation of mobile and stationary warehouse equipment. At the same time, the software to control automatic systems is becoming progressively simpler. This is not to say that everything will run automatically in the future, but a number of the afore-mentioned soft factors (access time, structural clarity, safety, etc.) are indeed met without further input. A good example of how the benefits of both worlds (automatic/special and manual/flexible) can be combined for warehouse employees is online navigation to a given rack location using “pick by light”.
4. Which rack layout and rack assignment?
Irrespective of whether the racks are filled manually or automatically, one topic remains, namely that of how to minimize transport distances in a warehouse layout. The longer the transport distances, the more resources are required and the longer it takes to make a product available at the correct workplace. In automatic warehouses, algorithms already optimize and analyze the transport distances when assigning goods to the rack compartments. In manual warehouses, the situation is often less clear-cut and it is not seldom that goods are simply placed where there happens to be space in a layout.
One possibility when planning the assignment of rack locations in a warehouse layout is to define rack zones. The A zone, for example, can then be reserved in the layout for products with a high turnover rate or where frequent access is expected. The positioning of this zone in the layout should then also provide for the shortest distances. The principle is illustrated in the following layout drawings.
Another possibility is to assign the rack locations in a layout such that products with a high turnover rate are placed in the lower shelves which are easiest to access. Products which are accessed less often are placed at higher levels in the layout. This is positive not only for the efficiency but also for safety. If planograms are produced for the individual racks, this will also maximize the transparency of the location assignments and further optimize the transport distances.
It is naturally advantageous to make use of software for the various aspects of warehouse planning and for the creation of corresponding warehouse layouts. Whether a single pallet or an entire pallet rack needs to be positioned according to the flow of materials in a factory, software can ensure that a decision is based on economic and planning considerations.
Further articles on the subject:
- The importance of space utilisation and design in your factory.
- Material flow planning to optimize logistics, production, and storage
- Floorspace dimensioning in factory planning
- What is the relation between Easter eggs and pallet shelves?
No problem, simply subscribe to our Blog-News!