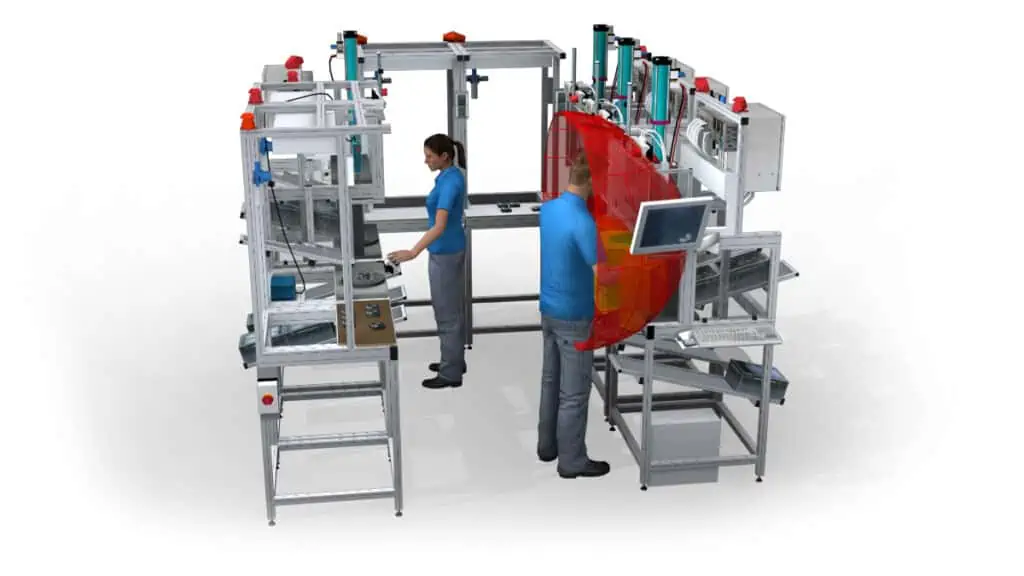
Montagelinien mit One-Piece-Flow (OPF-Arbeitssysteme) stehen in der Montageplanung hoch im Kurs. Große Vorteile werden in der Lean Production damit verbunden. In dem Zusammenhang sind insbesondere zu nennen:
- Kurze Durchlaufzeiten,
- geringe Bestände,
- gute Möglichkeiten der Automation auch mit Einsatz von (kollaborierenden) Robotern,
- kontinuierliche Produktion und nicht zuletzt
- eine gute Planbarkeit der Produktion durch die mit der Austaktung verbundene hohe Wiederholhäufigkeit.
In der optimalen Austaktung liegt jedoch auch die zentrale Anforderung in der Planung solcher Montagesysteme, gerade wenn es um wechselnde Stückzahlen oder variantenreiche Montagen geht. Manchmal erfolgt hierbei die Anwendung von Simulation, Montagelinien sind jedoch auch ohne solche dynamischen Computer-Modelle gut zu planen. Folgende 5 Schlüsselaspekte der Montageplanung sind in dem Zusammenhang zu bearbeiten.
Taktzeit
Die Planung einer One-Piece-Flow-Montage erscheint auf den ersten Blick einfach: Ausgehend vom Periodenbedarf eines Produktes wird die Rhythmik ermittelt, nach der ein Produkt die Montagelinie verlassen muss. Sie bestimmt die Taktzeit. Dazu ist dem Periodenbedarf die verfügbare Durchlaufzeit gegenüber zu stellen. In der Lean Production wird in dem Zusammenhang die Zeitdauer angesetzt, in der Kunden zyklisch Produkte benötigen. Sollen z. B. 3600 Stück pro Jahr hergestellt werden und es wird an 240 Arbeitstagen in 2 Schichten zu je 8 Stunden produziert, so stehen 3840 Stunden zur Verfügung. Alle 1,07 Stunden muss dann ein Produkt fertig sein, die resultierende Abruf-Taktzeit beträgt 64 Minuten. Soll nur eine Schicht genutzt werden, reduziert sich dieser Takt auf nur 32 Minuten.
Dieser Berechnungsansatz unterstellt, dass für jedes Produkt die gleiche Durchlaufzeit benötigt wird. Das funktioniert reibungslos, solange es sich um gleiche Produkte und damit um gleiche Aufwände für die Montage jedes einzelnen Produkts sowie einen über die Periode kontinuierlich benötigten Bedarf handelt. Daraus ergeben sich auch die Rahmen-Bedingungen für den effizienten Betrieb von Montagelinien.
Arbeitsinhalt (Kapazitätsbedarf)
Über den Takt der Produktionslinie hinaus ist bei der Montageplanung zu bestimmen, wieviel Arbeitsinhalt in der Montage jedes Produkts steckt. Zentral ist dabei der Zeitbedarf für die Ausführung der Montageaufgaben. Dieser ist ungleich schwieriger zu ermitteln. Schließlich hängt er von der eingesetzten Montage-Technologie ab. So kann beispielsweise ein vollautomatisierter Prozess mehrere Teile gleichzeitig fügen, wofür ein Mitarbeiter übernatürliche Fähigkeiten aufzubringen hätte. Auf der anderen Seite sind hoch automatisierte Betriebsmittel entsprechend spezialisiert und oft teuer und unflexibel. Auch aus diesem Grund favorisieren Lean-Production-Ansätze sogenannte Low-Cost-Automation.
Low-Cost-Automation
Charakteristisch ist das Automatisieren von Mikrotransporten mit Hilfe von Schwerkraft.
- Geneigte Rollenbahnen,
- schräg angestellte Behälter,
- Magazine u. ä. Lösungen
führen die Hauptbaugruppe und Bauteile automatisch im One-Piece-Flow nach, während Mitarbeiter Montageschritte ausführen, die sich nicht kostengünstig automatisieren lassen. Folgt man diesem Prinzip, konzentriert sich die Montageplanung zunächst auf die zeitliche Analyse der notwendigen Fügeprozesse unter der Annahme einer manuellen Ausführung. Hilfreich sind in diesem Zusammenhang Methoden der manuellen Montageplanung, die standardisierte Prozessbausteine anbieten. Aus ihnen ist der Arbeitsablauf regelbasiert zusammenzusetzen. Weltweit standardisiert ist hierzu MTM. Die aus der Analyse entstehende Zeitsumme widerspiegelt den erforderlichen Kapazitätsbedarf für die Mitarbeiter und Mitarbeiterinnen in der Montage.
Austaktung von Montagelinien
In der Austaktung (oder auch Abtaktung) ist der ermittelte Kapazitätsbedarf so auf Stationen (Arbeitsplätze der Montagelinie) zu verteilen, dass ihre Auslastung möglichst hoch ist. Pro Station steht die Taktzeit zur Verfügung. Ist der Kapazitätsbedarf größer als die Taktzeit, muss er zwischen einzelnen Stationen aufgeteilt werden. Nur dann ist eine Montagelinie erforderlich, sonst genügt ein einzelner Arbeitsplatz.
In der Lösung von Austaktungs-Problemen (line balancing) liegen wesentliche Herausforderungen bei der Montageplanung. Denn i. d. R. sind die einzelnen Schritte der Montage-Aufgabe nicht gleichmäßig auf die Takte zu verteilen. Daraus ergeben sich Engpässe in der Linie. Dem gegenüber steht eine zunehmende Variantenvielfalt der Produkte, in deren Ergebnis sich die Arbeitsinhalte zwischen den im One-Piece-Flow aufeinander folgenden Teilen unterschiedlich ausprägen. Beide Effekte können sich im Montagesystem gegenseitig verstärken oder abmildern. Zwar versprechen Optimierungsstrategien unter Einsatz von Simulation kompletter Montagelinien Lösungsansätze, dennoch ist die Erstellung und Pflege entsprechender Computer-Modelle für die Praxis vieler Unternehmen selbst in Anwendung von Industrie 4.0 schlichtweg zu aufwändig. Es dominieren deutlich einfachere Modelle zur Planung der Austaktung, vgl. Abbildung.
Arbeitsteilung
Flexible Arbeitsteilung gilt unter vielen Aspekten als Geheimtipp zur Realisierung schlanker Produktion. Sie mildert vor allem zeitliche Restriktionen in der Austaktung, indem die Montageschritte nicht starr auf Stationen der Linie zugewiesen werden, sondern für die Mitarbeiter und Mitarbeiterinnen situativ erschließbar vorgehalten werden. Dies „erkauft“ man sich durch Planung von Puffern im Montagesystem, welche nach dem FiFo-Prinzip arbeiten und so die Reihenfolge im One-Piece-Flow sichern. Mit Puffern provoziert man quasi ein kontinuierliches Überangebot an Arbeit für die Ressourcen in der Montagelinie. Die Arbeitsinhalte in den Puffern sind dabei abwechselnd abzuarbeiten – leert sich ein Puffer, droht ein anderer überzulaufen. Durch diese Methode ist die Auslastung der unterschiedlichen Ressourcen im Montagesystem immer gesichert. Zudem sind inter- und intraindividuelle Leistungsunterschiede gut zu kompensieren.
Als Grundprinzipien der Arbeitsteilung gelten Art- und Mengenteilung.
- Bei Artteilung wird die Montage-Aufgabe bzgl. der Tätigkeitsart (z. B. Schrauben, Kleben) zwischen Ressourcen verteilt.
- Bei Mengenteilung wird die Aufgabenmenge verteilt, so das sich mehrere gleichartige Aufgaben (parallel) ergeben.
Durch Kombination dieser beiden Prinzipien entstehen vielfältige Lösungsansätze auch für schwierige Austaktungssituationen. In Verbindung mit flexiblen Arbeitsganggrenzen (Schwimmen im Takt) oder dem situativen Wechsel zwischen Montage-Aufgaben im Haupt- und Nebenfluss (z. B. Vor- und Endmontagen) bleibt auch ein variantenreicher Produktmix im One-Piece-Flow unter angemessener Auslastung und Durchlaufzeit beherrschbar.
Verwandte Themen:
- Was leistet Cardboard Engineering und was nicht?
- Was ist Inselfertigung?
- Fließfertigung oder Werkstattfertigung?
- 6 Maßnahmen um den Engpass in der Produktion aufzulösen
Kein Problem, einfach für unsere Blog-News anmelden!