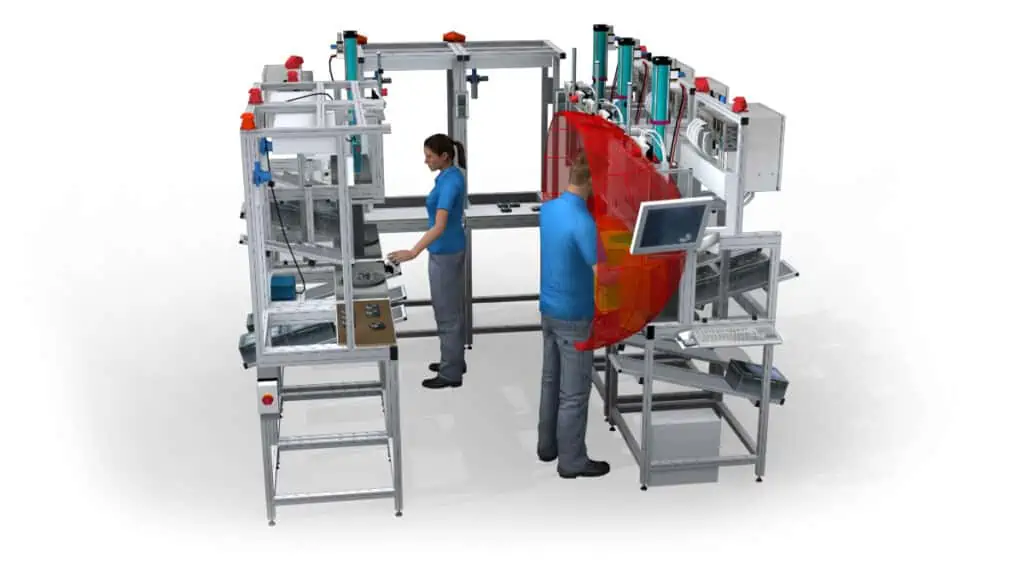
Assembly lines within one-piece-flow (OPF work systems) are very popular in assembly planning. Great advantages are associated with this in lean production. In this context, particular mention should be made of the following:
- Short lead times,
- low inventories,
- good possibilities of automation also with the use of (collaborating) robots,
- continuous production and last but not least
- good planning of production due to the high repetition frequency associated with the tacting.
However, the central requirement in the planning of such assembly systems also lies in the optimal synchronization, especially when it comes to changing quantities or variant-rich assemblies. Sometimes simulation is used for this, but assembly lines can also be planned well without such dynamic computer models. The following 5 key aspects of assembly planning have to be dealt with in this context.
Takt time (Cycle time)
The planning of a one-piece-flow assembly appears simple at first glance: Based on the period requirements of a product, the rhythm according to which a product must leave the assembly line is determined. This determines the tact time. To do this, the period requirement must be compared with the available cycle time. In Lean Production, the period of time in which customers cyclically require products is used in this context. If, for example, 3600 pieces are to be produced per year and production takes place on 240 working days in 2 shifts of 8 hours each, then 3840 hours are available. A product must then be ready every 1.07 hours, the resulting call-off cycle time is 64 minutes. If only one shift is to be used, this cycle is reduced to only 32 minutes.
This calculation approach assumes that the same cycle time is required for each product. This works smoothly as long as the products are the same and therefore the effort required to assemble each product is the same, and the demand is continuous over the period. This also results in the framework conditions for the efficient operation of assembly lines.
Work content (capacity needs)
Beyond the production line cycle, assembly planning involves determining how much work content is involved in the assembly of each product. Central to this is the time required to perform the assembly tasks. This is much more difficult to determine. After all, it depends on the assembly technology used. For example, a fully automated process can join several parts at the same time, for which an employee would have to muster supernatural skills. On the other hand, highly automated equipment is correspondingly specialized and often expensive and inflexible. This is another reason why lean production approaches favor so-called low-cost automation.
Low-cost automation
Characteristic is the automation of micro transportations with the help of gravity.
- Inclined roller conveyors,
- inclined containers,
- magazines, etc. solutions
automatically track the main assembly and components in a one-piece flow, while workers perform assembly steps that cannot be automated cost-effectively. If this principle is followed, assembly planning initially focuses on the time analysis of the necessary joining processes, assuming manual execution. In this context, manual assembly planning methods that offer standardized process modules are helpful. The work sequence is to be assembled from them in a rule-based manner. MTM is standardized worldwide for this purpose. The time sum resulting from the analysis reflects the necessary capacity requirements for the employees in assembly.
Assembly line balancing
Using line balancing, the determined capacity needs are to be distributed to stations (work centers of the assembly line) in such a way that their capacity utilization is as high as possible. The takt time is available for each station. If the capacity need is greater than the cycle time, it must be distributed between individual stations. Only then is an assembly line necessary, otherwise, a single workstation is sufficient.
The solution of line balancing problems is a major challenge in assembly planning. As a rule, the individual steps of the assembly task cannot be distributed evenly over the cycles. This results in bottlenecks in the line. On the other hand, there is an increasing number of product variants, which results in different work contents between the parts that follow one another in the one-piece flow. Both effects can reinforce or mitigate each other in the assembly system. Although optimization strategies using simulation of complete assembly lines promise approaches to solutions, the creation and maintenance of corresponding computer models are simply too time-consuming for the practice of many companies, even in the application of Industry 4.0. Significantly simpler models for planning the line balancing dominate, see figure.
Work division in assembly lines
From many aspects, flexible division of labor is considered an insider’s tip for implementing lean production. Above all, it alleviates time restrictions in synchronization by not assigning assembly steps rigidly to stations on the line but instead making them available to the employees according to the situation. This is “bought” by planning buffers in the assembly system, which work according to the FIFO principle and thus ensure the sequence in the one-piece flow. With buffers, one virtually provokes a continuous oversupply of work for the resources in the assembly line. The work contents in the buffers are to be processed alternately – if one buffer empties, another one threatens to overflow. This method ensures that the various resources in the assembly system are always utilized to capacity. In addition, inter-, and intra-individual performance differences can be compensated well.
The basic principles of division of labor are division per type of process and quantity division.
- With division per kind of process, the assembly task is distributed between resources with regard to the type of activity (e.g. screwing, gluing).
- In the case of quantity division, the task quantity is distributed so that several tasks of the same type (parallel) result.
Combining these two principles results in a wide range of solutions, even for difficult de-blocking situations. In conjunction with flexible work cycle limits (floating in cycles) or the situational alternation between assembly tasks in the main and secondary flow (e.g. pre-, and final assemblies), even a product mix with many variants in the one-piece flow remains manageable with appropriate capacity utilization and throughput time.
Related topics:
- 6 measures to resolve the bottleneck in production
- What is a production cell?
- What means Cardboard Engineering?
- Job shop production vs. production line?
No problem, simply subscribe to our Blog-News!