When one stops all, a question of capacity
You certainly know the following situation: Although your production permanently works with extra hours and extra effort, the delivery times of your enterprise are often not observed. The reason can be bottlenecks in your production system. But what are bottlenecks, and why do they lead to such serious problems for the entire enterprise?
“Delivery delay despite overtime – are you familiar with this?”
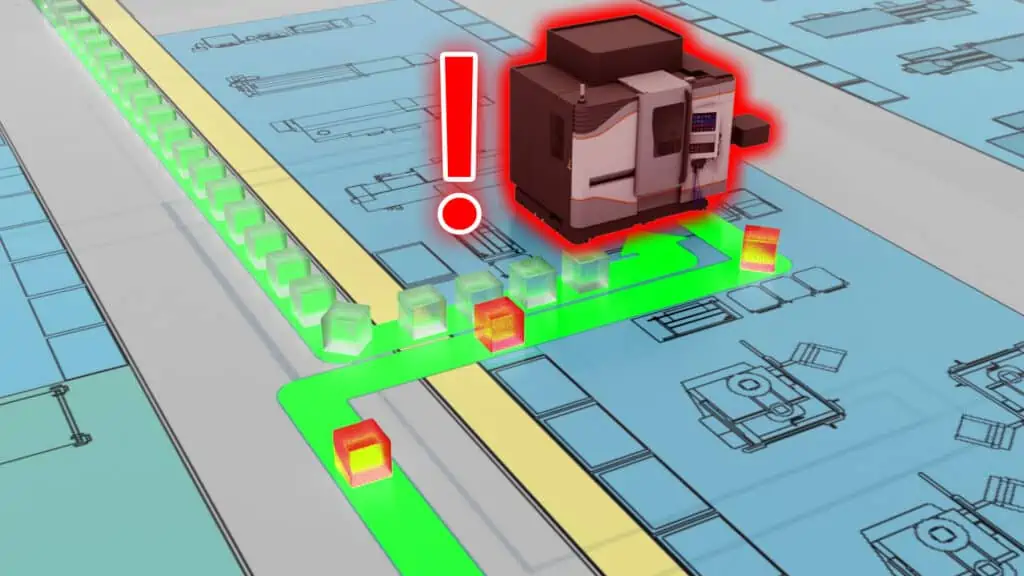
The answer is simple: We speak of a bottleneck if the demand exceeds the available capacity of an item of your manufacturing equipment. But why individual machines have such a negative effect on your entire production system? This question can vividly be answered by way of a well-known example: The walking tour of a scout group.
A scout group is walking in single file on a narrow path to the scout camp. After a short time, it is noticed that the gaps between the children are growing wider and wider in some places, whereas they are all bunched up together elsewhere along the line.
The reason is the different speeds the children are moving. The group wants to arrive at the finish as a unit; as the solution, the order of the children was changed. Now the slowest child is in the first position and determines the speed for the whole group. The example of the scout group can be transferred exactly to our production system. The capacity and thus the throughput of a bottleneck determines the throughput for the whole production system as far as the bottleneck parts are concerned.
“One hour lost at the bottleneck means one hour lost for the entire production system.”
Identify a bottleneck in production
This is the reason why the production program must be matched primarily to the capacity of the bottleneck, i.e. the bottleneck of the system. In a metaphorical sense: The bottleneck should be placed in the first position as in the example with the scout group.
If we don’t and burden the production system with too many jobs, a tailback would be the result, leading to increased inventories and longer cycle times – similar to the chain of the scouts which became longer and longer.
This is the reason why it is initially essential to identify the bottleneck or bottlenecks in the production. Bottlenecks are often already known because delayed delivery and high inventories only occur in case of bottleneck products. ERP systems are used today to support us in analyzing bottlenecks or identifying short capacities. Various tools to identify bottlenecks are also provided in the environment of the lean production management.
If a bottleneck is already identified, the question arises as to measures how to remove it. This topic should definitely be addressed, because the costs of appropriate measures are usually significantly lower than the costs incurred due to the bottleneck. Why is that? The throughput of the bottleneck determines the overall throughput of the production – one lost hour at the bottleneck results in one lost hour for the whole production system. The lost work can no longer be compensated. Losses at the bottleneck thus act directly on the costs of the entire system; the costs incurring in conjunction with the measures to remove the bottleneck should only cost a fraction.
Ways to eliminate the bottleneck in production
The following measures should be mentioned in this context:
1. Avoid downtimes
- Adapt the shift system of the bottlenecks accordingly; they should operate day and night
- Cover pause times by assigning reserve personnel
- Use additional operating personnel
- Reduce the loading times, e.g. by loading a machine during the processing time by way of a pallet changing table
2. Outsourcing
- Farming out of jobs or services to external service providers or other manufacturers
3. Use alternative manufacturing equipment
- For example, use alternative machines, systems and workplaces to perform work and services of the bottlenecks. It is not relevant whether the manufacturing equipment does not work as efficiently (fast) as the bottlenecks – it is a matter of capacity increase of the entire production system.
4. Reduce rejects in the production of the bottleneck parts
- Place test processes upstream the bottleneck to prevent nonconforming parts to be processed
- Mark bottleneck parts as such and apply additional safety measures and greater care where necessary
5. Satisfy only the actual demand
- Do not produce stock items; only process the immediate demand of the customers.
6. Adapt the lot sizes
- Amalgamate setup and maintenance processes.
- Where necessary, increase the lot size at the bottlenecks to minimize the setup times.
In addition to measures to increase the production capacity, the production program or complete system is to be matched to the capacity of the bottlenecks. The challenge is to plan an ideal production rate for manufacturing and assembly operations, i.e. not too many products but at the same time not too few, so as to achieve maximum utilization at the bottlenecks and maintain a continuous and balanced material flow with low inventories and short overall cycle times. This can be achieved by way of different methods for production control within the framework of production management – bottleneck control, ConWIP, and Kanban are mentioned here only as examples.
Related topics:
- How important is lead time in factory planning?
- Material flow planning to optimize logistics, production, and storage
Do not miss anything more and subscribe to our blog:
No problem, simply subscribe to our Blog-News!