Vom Wertstrom zum Layout! Klingt logisch und ist logisch. Zentraler Gedanke ist das sogenannte Line-back-Prinzip. Es beinhaltet eine Gestaltung des Fabriklayouts von innen nach außen. Oder anders formuliert: Die Fabrikplanung ist vom Zentrum der Wertschöpfung ausgehend hin zur Peripherie zu entwickeln.
Was ist das Problem?
Wenn dieses Konzept so eingänglich und logisch ist, warum verfolgen es dann nur Wenige? Warum entstehen Fabrikplanungen häufig ausgehend vom Gebäude, dessen Raum dann sukzessive befüllt wird?
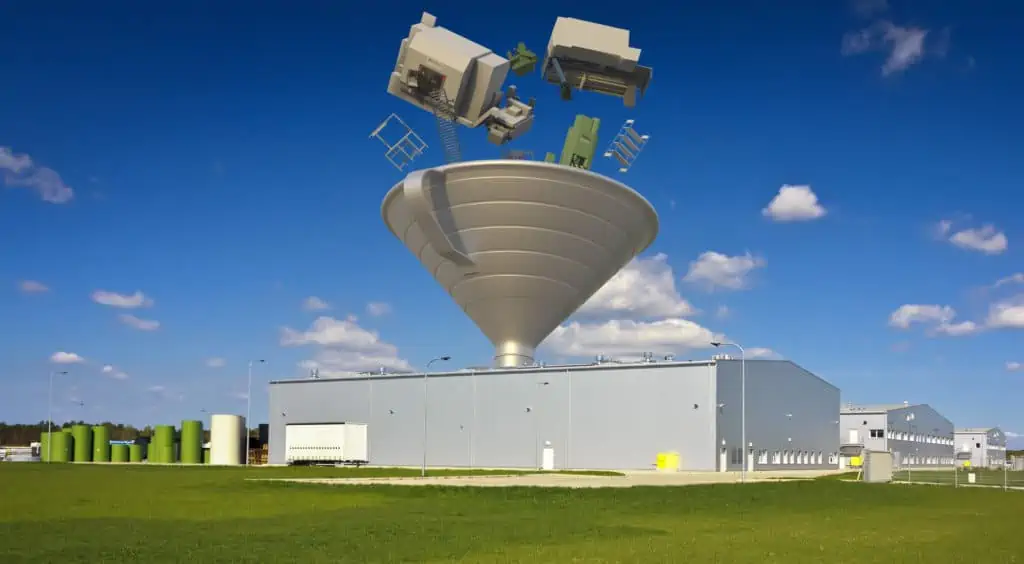
Eine Antwort scheint offensichtlich: Zuallererst stehen die Investitionskosten im Fokus, wenn es um das Bauwerk und dessen fixe Ausrüstungen geht. Denn das Gebäude samt TGA stellt i. d. R. den größten Kostenblock dar und der soll nun mal möglichst gering sein. So wird jedoch die Peripherie gleich zu Beginn zur Restriktion:
- Wo kommt die Lüftungstechnik hin?
- Wie sind die sanitären Anlagen möglichst kostengünstig im Bauwerk einzubringen?
- Wie kommen leitende Angestellte möglichst schnell vom Parkplatz in ihr Büro?
- Wie kann das Bauwerk konstruktiv optimiert werden, um die Kosten zu minimieren?
- Wie kann die Grundstücksfläche möglichst kostengünstig ausgelastet werden?
Dem Line-back-Prinzip folgend würde man umgekehrt fragen: Welche Investitionssumme kann eine optimale Produktionsstruktur stemmen? Ist es nicht günstiger, in einem anforderungsgerechten, ggf. teureren Baukörper eine effiziente Fabrikstruktur zu betreiben, als in einem günstigen Allzweckbau inneffiziente Strukturen zu akzeptieren?
Diese Fragen mögen im Einzelfall schwierig zu beantworten sein. Jedoch gilt generell, dass günstige Betriebskosten eine Investition schneller zu refinanzieren helfen.
Ein Beispiel zur Illustration
Unsere Urgroßväter wären nie auf die Idee gekommen, ihr Haus ohne Keller und Dachboden zu planen, weil es im Haushalt immer Dinge gab und gibt, die genau dorthin müssen. Vielleicht sind es nicht die wichtigsten Dinge. Nur wer weiß schon, was in 60 Jahren für die Urenkel einmal wichtig ist?
Das kostenoptimierte, moderne Einfamilienhaus dagegen steht auf einer Bodenplatte, darauf direkt die erste Wohnetage. Das Dachgeschoss ist meist vollständig in den Wohnraum integriert. Es dauert nach dem Einzug oft nur wenige Monate, bis sich im Garten das erste Holzhäuschen für dies und jenes entdecken lässt; nach Jahren entwickeln sich die Behelfslager zu respektablen baulichen Anlagen. Diese jedoch sind aufgrund des i. d. R. restriktiven Baurechts stets nur als Kompromiss zu Boden oder Keller zu errichten; wertvolle Grundstücksfläche für kreative Gartengestaltung, Erholung und Spiel geht verloren. Und man wird trotzdem nass, wenn man bei Regen von dort etwas im Haus benötigt. „Inhouse“-Alternativen sind meist noch unsinniger, denn wer will schon z. B. die Kartoffeln im Heizraum lagern?
Ein Beispiel aus der Fabrikplanung
Auch in der Fabrikplanung gibt es immer wieder scheinbare Randschauplätze, die beim großen Kostenpoker zu wenig Beachtung finden. Nehmen wir das Lager: Es kostet wertvolle Fläche. Also wird man versuchen, es so klein und günstig wie möglich zu halten. So landet es z. B. in einem Kaltbau neben dem Produktionsgebäude. Dort kann man dann auch ein paar mehr Regale kostengünstig unterbringen.
Die Folge ist, dass Material von und zum Lager transportiert und in der Produktion zwischengelagert werden muss. Dafür benötigt man nicht nur Wege und Flächen, sondern auch zusätzliches Handling. Bei langen Wertströmen mit vielen verketteten Arbeitsschritten mag das eine beherrschbare Lösung sein. Schaut man nun ein paar Jahre in die Zukunft, ändert sich das Szenario:
- Der Eigenfertigungsanteil wird sich tendenziell reduzieren,
- die Variantenvielfalt exponentiell steigen.
- Fertigungsstufen entfallen,
- der C-Teile-Anteil steigt,
- der Wertstrom wird kürzer.
Die Frequenz der Ein- und Auslagerungen steigt dadurch massiv an. Weiterhin müssen viel mehr Transporte pro Zeiteinheit in die Produktion getätigt werden, die nunmehr reinen Montagecharakter hat. Temperaturempfindliche Bauteile müssen ggf. vollständig innerhalb der Produktion gelagert werden. Das „billige“ Kaltlager außerhalb der Halle wird zum Betriebskostentreiber. In nur wenigen Betriebsjahren sind die Kostenvorteile ggü. der zweifellos deutlich höheren Investition in ein flexibles produktionsnahes Lagersystem mit mehreren Ein- und Auslagerschleusen verpufft.
Wie Wertstrom und Layout zusammen hängen
Geht man den Weg konsequent vom Wertstrom zum Layout, werden jedem Prozess-Schritt Ressourcen zugewiesen. Ressourcen sind z. B. Anlagen, Montageplätze oder ganze Fertigungsbereiche, je nach Auflösungsgrad des betrachteten Fabrikmodells. Bringt man deren Platzbedarfe und die resultierenden Transporthäufigkeiten in ein maßstäbliches Layout, erhält man eine Darstellung ähnlich einem Sankey-Diagramm.
Ändert man nun den Wertstrom z. B. mittels einer Szenario-Planung – wird er wie im o. a. Beispiel kürzer – so verändern sich zwischen den beteiligten Ressourcen auch die Materialfluss-Verknüpfungen und deren Transportintensitäten. Hierdurch würde man für dieses Beispiel feststellen, dass sich die Transportintensität zwischen Lager und Produktion im Zukunftsszenario mit kürzeren Wertströmen erhöht. So steigt der Transportaufwand hier um 15 % ggü. der Situation mit dem derzeitigen langen Wertstrom, wo mehrere Fertigungsschritte nacheinander durchlaufen werden.
Nutzt man für diese Untersuchung ein digitales Fabrikmodell mit entsprechendem Kennzahlencockpit, lassen sich Auswirkungen einer Änderung der Wertstromstruktur auf das Layout schnell bewerten. So ist der Unterschied in den Transportaufwänden und –kosten für die Layoutvariante mit externem Kalt-Lager ggü. einem zentralen AKL leicht zu quantifizieren. Im hier gezeigten Beispiel sehen wir, dass das Layout mit integrierten Lagerbereich ggü. der Kaltlager-Lösung zu 28 % geringeren Transportaufwänden beim aktuellen, langen Wertstrom führt. Darüber hinaus ist zu sehen, dass diese Lösung auch robust ggü. den in Zukunft zu erwartenden kürzeren Wertströmen ist: Auch hier ist der Vorteil in den Transportaufwänden immer noch auf 28 % zu beziffern.
Die von den Investitionen her kostspieligere Lösung erweist sich also aus Wertstromperspektive nicht nur aktuell, sondern auch zukünftig betriebskostenärmer. Das Einsparpotenzial kann nun gegen den Investitionsmehraufwand über die Standzeit des Layouts gerechnet werden. Das Risiko einer Fehlentscheidung sinkt.
Wie funktioniert das in der Planungspraxis?
Wertströme liegen in den meisten praktischen Fällen in einer digital nicht verwertbaren Form vor. Dies ist nicht weiter verwunderlich, da das Konzept der Wertstromskizzen (engl. Value Stream Mapping) von seinen Entwicklern in der von Toyota übernommenen ursprünglichen Form postuliert wird:
„Zeichnen Sie den Wertstrom von Hand mit dem Bleistift“ als „Kommunikationsmittel für Menschen, die ihr Können aus Praxiserfahrungen ableiten.“
Rother, M.; Shook, J.: SEHEN LERNEN mit Wertstromdesign die Wertschöpfung erhöhen und Verschwendung beseitigen. Aachen: Lean Management Institut, 2004.
Das Skizzieren von Wertströmen folgt also keiner streng algorithmierbaren Logik, sondern dient dem Schaffen von Grundverständnis für den Materialfluss von Rampe zu Rampe und den ihn steuernden Informationsfluss.
Folglich ist es für eine digitale Auswertung von Wertströmen i. d. R. notwendig, die Wertstrom-Maps in eine Computer-verständliche Form zu bringen. Für die Layoutgestaltung relevant ist dabei nur der untere Teil der Wertstromskizze, der Warenstrom. Dort werden notwendige Arbeitsschritte samt ihren Zykluszeiten, deren Ressourcen und ihre logistische Verknüpfung beschrieben, wie sie zur Herstellung der Menge 1 einer Produktfamilie notwendig sind.
Die Warenstrom-Notation ist unabhängig davon, ob es sich bei dem betrachteten Wertstrom um einen Ist- oder einen Sollzustand handelt. Sie ähnelt in ihrer Struktur den Prozesskästen im Wertstrom, jedoch werden auch ortsfeste logistische Operationen (Einlagern, Auslagern, Bereitstellen) in Prozesskästen beschrieben. Dies ist notwendig, da jeder Operation ein Platzbedarf im Layout zuzuweisen sein muss. Der Platzbedarf repräsentiert die sogenannte Ressource im Layout; das Objekt also, was den Platz benötigt. Damit wird auch klar, wieso in der Warenstrom-Notation keine extra Symbolik für verschiedene Lager- und Puffereinrichtungen (KANBAN-Regale, FIFO-Bahnen etc.) notwendig wird. Sie ist eine reine Prozess-Sicht, die Ressourcen werden im verknüpften Layout spezifiziert.
Für das Transportieren werden Pfeile verwendet. Hierbei repräsentiert jeder Pfeil einen Transport einer bestimmten Häufigkeit mit einem bestimmten Transportmittel. Der Warenstrom-Graph wird mit einem digitalen Werkzeug erfasst. Das kann dank Touch-Technologie heute genauso intuitiv am Tablet-PC erfolgen, wie es bei Toyota seinerzeit mit Papier und Bleistift erfolgte.
Das Warenstrom-Werkzeug stellt einen direkten Bezug zu einem digitalen Layout her, es versorgt das Layout mit Materialflussdaten. Daraus kann
- zum Einen ein layoutbezogenes Sankey-Diagramm berechnet;
- zum Anderen ein Algorithmus zur Anordnungsoptimierung gespeist und
- zum Dritten die logistische Last für das Layout ermittelt werden.
Somit steht ein für die Anordnungsplanung und Layoutbewertung geeignetes digitales Fabrikmodell für das Beantworten der oben am Beispiel erläuterten Fragestellungen zur Layoutstruktur bereit.
Welchen Nutzen hat die Vorgehensweise vom Wertstrom zum Layout?
Viele Layoutworkshops in der Praxis werden mit einfachen Schablonen anhand ausgedruckter CAD-Pläne durchgeführt. Die Arbeitsweise mit so einfachen Mitteln hat den unschlagbaren Vorteil, dass jeder einfach mitarbeiten kann. Demselben, auf Einfachheit gerichteten, partizipativen Konzept folgt das Skizzieren von Wertströmen. Beide Verfahren behandeln den Gegenstandsbereich der Fabrikplanung aber in jeweils einer relativ isolierten Sicht,
- einer Layout-Sicht und
- einer Prozess-Sicht.
In der Layout-Sicht bleiben die prozessualen Zusammenhänge intransparent, man konzentriert sich beim Planen auf geometrische Zusammenhänge und muss den Fluss „aus dem Bauch heraus“ einschätzen. Bei der Prozess-Sicht hingegen bleibt die Geometrie dem „Bauchgefühl“ überlassen.
Durch integrierte Betrachtung von Prozess und Layout, hat man ausgehend von einem aus Perspektive des Wertstroms optimalen Prozesses die einzigartige Möglichkeit, das für den Prozess notwendige Layout ebenso im Fokus zu behalten. Wechselwirkungen können leichter erkannt und mit geeigneten „Stellschrauben“ aus beiden Sichten synchron behandelt werden.
So wurden beispielsweise in der Planungspraxis des Autors zahlreiche Workshops nach diesem Verfahren durchgeführt, wobei erstaunlich oft erst in der Betrachtung der einzelnen Prozessschritte klar wurde, wofür Alles man Platz im Layout vorsehen muss. Auf der anderen Seite konnte in vielen Ist-Layouts erkannt werden, dass Platz für Dinge ver(sch)wendet wurde, die mit dem Prozess
- recht wenig oder
- gar nicht oder
- nur in deutlich geringerer Intensität verknüpft oder
- schlichtweg überdimensioniert waren.
Die besten Effekte wurden hierbei bei der Betrachtung höher aufgelöster Layouts erreicht, also z. B. auf der Ebene von Fertigungsplatzgruppen oder Montageinseln. D. h. insbesondere dort, wo die Zentren der Wertschöpfung liegen, können durch das Vorgehen vom Wertstrom zum Layout deutlich besser abgesicherte Layout-Entwürfe realisiert werden.
Wie kann ich das einfach umsetzen?
Die hier erörterte Verknüpfung von Wertstrom und Layout lässt sich in der einfachen analogen Form nicht bewältigen, die Wertstrom- oder Layoutskizzen mit Papier und Bleistift eröffnen. Ein Werkzeug zur digitalen Fabrikplanung ist nahezu unumgänglich. Alle hier dargestellten Erfahrungen basieren auf Anwendung von visTABLE®, einem partizipativen Planungswerkzeug, was seinen Ursprung in Entwicklungen renommierter Forschungseinrichtungen in der Schweiz und in Deutschland hat.