Ideal steht in der Philosophie sowie in der Technik für ein Muster an Vollkommenheit. Namensgeber ist die Idee (lat. idea), der Gedanke an das absolut Vollkommene also. Gleichsam schwebt das Ideal im Raum des Unerreichbaren und wird von Pragmatikern daher gern als ambitioniertes Ziel eingeordnet, was in der Praxis nach und nach erodiert.
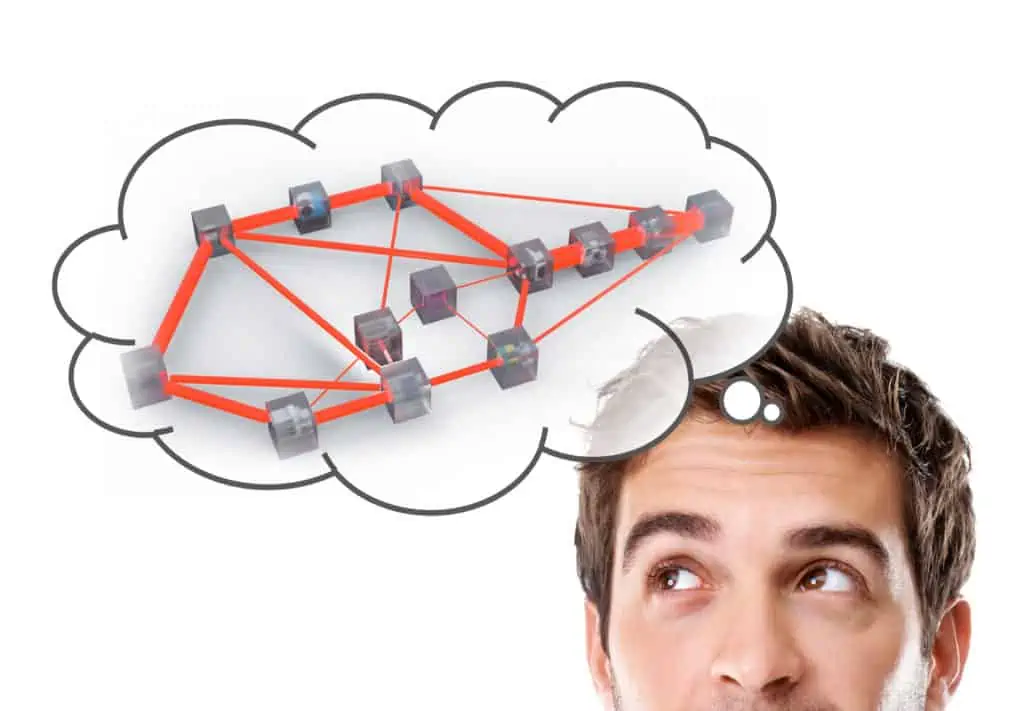
Etwa diesem Bild folgt die Theorie der Layoutplanung. Es gibt eine Vorstellung davon, wie das optimale Fabriklayout aussieht. Dieses Ideallayout (auch: Ideal-Layout) kann berechnet werden. Es beschreibt eine Anordnung der Layoutobjekte (z. B. Maschinen, Anlagen, Produktionsbereiche), wobei alle wesentlichen Zielgrößen der Layoutplanung ihren Bestwert erreicht haben.
Schon hier beginnt der Pragmatismus zum Ideallayout: Was sind denn die wesentlichen Zielgrößen? Dies führt auf die Frage, welche Freiheitsgrade durch Layoutplanung überhaupt beeinflussbar sind und damit zu der Messgröße, mit der sich das Ideallayout von anderen Layoutvarianten unterscheiden und so als ideale Lösung herausstellen lässt.
Und es geht pragmatisch weiter: Dem Ideal gegenüber steht die Realität. Die Realität erzeugt Restriktionen, die das Ideal in seiner praktischen Umsetzung blockieren. Welche Restriktionen sind das? Ist es überhaupt sinnvoll, ein Fabriklayout ohne Restriktionen zu entwerfen? Unser Video zeigt, dass und wie es funktioniert:
Hier in diesem Blog wollen wir den Fokus auf die Methodik und die praktische Bedeutung des Ideallayouts in der Fabrikplanung richten.
Wodurch ist das Ideallayout ideal?
Betrachtet man die Freiheitsgrade in der Layoutplanung ganz formal, so sind diese recht überschaubar. Gegeben ist eine Menge an dimensionierten Anordnungsobjekten, die optimal zueinander zu positionieren sind. Die Ausdehnung der Objekte ist durch die Dimensionierung bereits bestimmt. Einzig gestaltbare Größe ist also der Abstand zwischen den Objekten. Hierbei wird deutlich, dass die Gestalt der Objekte auf ihren Abstand zueinander einen nicht unerheblichen Einfluss hat.
Der Platzbedarf als Kostentreiber
Ist eine Anordnung also ideal, bei der zwischen allen Objekten der Abstand gleich Null ist? Denn in dem Fall ist wohl davon auszugehen, dass die für alle Objekte benötigte Gesamtfläche als Kostentreiber ein Minimum erreicht. Bei einem Puzzle ist das beispielsweise so. Hierbei ist jedoch durch die Form und das Bild der Anordnungsobjekte für jedes Puzzle-Teil i. d. R. nur genau eine Position ideal. Sind Formen dagegen variabel, können für dieselbe Menge an Anordnungsobjekten verschiedene Anordnungen gefunden werden, bei denen die Objektabstände gleich Null sind. Folglich ist eine geometrisch dichte Anordnung aller Objekte nur eine notwendige Randbedingung eines Ideallayouts, keine hinreichende.
Der Einfluss der Logistik
Insofern ist es erforderlich, ein weiteres Maß für die Beurteilung der Vollkommenheit eines Layoutentwurfes heran zu ziehen. Die Betrachtung von Kostentreibern im Produktionsprozess in Verbindung mit dem Objektabstand führt sehr schnell auf Materialfluss und Logistik. Denn wird zwischen einzelnen Maschinen viel Transportvolumen nötig, so spielt ihr Abstand zueinander eine größere Rolle, als der Abstand von Objekten mit geringem Transportvolumen. Darum sollte man das Transportvolumen als Gewichtung für den Objektabstand heranziehen. Alle Anordnungsobjektpaare erhalten so eine Priorität abgeleitet aus dem Materialfluss.
Sind die Transportvolumina jedoch in weiten Teilen gleich, wird es bei dieser Priorisierung Gleichrangigkeit geben. Das Ideallayout wird dann mit Hilfe einer weiteren Messgröße bestimmbar, der Anzahl der Materialflussbeziehungen der Anordnungsobjekte zueinander. Der terminus technicus dazu ist der Kooperationsgrad. Er beschreibt vereinfacht ausgedrückt, inwieweit sich ein Materialfluss-System linear in Form einer Kette darstellt oder eben mehr als Netz.
Der Transportaufwand als Messlatte für das Ideallayout
Führt man all das zusammen, entsteht eine Priorität für die Anordnung der Objekte zueinander, die sich aus Transportvolumen und logistischer Vernetzung speist. Diese wird beim Layoutentwurf nutzbar durch Anwendung sogenannter Aufbau- oder Vertauschungsverfahren. Dabei handelt es sich um Heuristiken, die den Layoutplaner durch den Entwurfsprozess führen.
Im Ergebnis entsteht ein dicht gepackter „Flickenteppich“, ein Blocklayout. Dessen Güte wird mit dem sogenannten Transportaufwand bewertet. Er berechnet sich aus dem Produkt aller Transportvolumina mit den jeweils zu überbrückenden Distanzen zwischen den angeordneten Objekten. Zur Bestimmung dieser Distanzen wird der einfache Abstand der Flächenschwerpunkte herangezogen. So entsteht eine einfache Messgröße. Variiert man nun die Anordnung der Objekte, ändert sich der Transportaufwand. Je geringer er ausfällt, umso dichter ist die gefundene Anordnung am Ideallayout.
Wie entsteht ein Ideallayout?
So einfach das Konzept des Ideallayouts auch ist, für seine Entwicklung sind ein gewisses Datengerüst und etwas Methodik erforderlich. Insofern stellt sich natürlich die Frage nach der Wirtschaftlichkeit der Ideallayout-Planung. Vorweg gesagt: Es lohnt sich. Denn die zur Ideallayout-Planung erforderlichen Daten und Methoden können in der Fabrikplanung durchgängig weiter genutzt werden. Das beinhaltet auch die Optimierung vorhandener Fabriklayouts. Schauen wir darum auf die Vorgehensweise.
Schritt 1: Das Funktionsschema der Fabrik
Bei der Ideallayout-Planung folgt man dem Grundsatz „Design follows function“. Ausgangspunkt ist das sogenannte Funktionsschema der Fabrik. Es beschreibt den prozessualen Zusammenhang der Anordnungsobjekte im Fabriklayout. Dazu analysiert man die technologisch notwendigen Abläufe für die Erzeugung aller Outputs der Fabrik, die mit relevantem logistischem Aufwand verbunden sind.
Eine geeignete Datenquelle für das Funktionsschema zum Ideallayout sind die Soll-Wertströme der Fabrik. D. h. man benötigt alle Produktfamilien in ihren idealen Produktionsabläufen. Die dabei durchflossenen Technologien bilden die in der Fabrik anzuordnenden Ressourcen, z. B. in Form von Fertigungsbereichen (Maschinengruppen, Anlagen, Montagelinien etc.).
Schritt 2: Das Sankey-Diagramm
Um die Transportvolumina zu bestimmen, sind konzeptionelle Annahmen bzgl. der Logistik hilfreich. Man kann natürlich auch vom reinen Massen- oder Volumenstrom zwischen den Ressourcen ausgehen. Da das Wertstromdesign jedoch bereits weitgehend Ziel-Transportlosgrößen definiert, ist zumindest die Berechnung der Transportintensitäten zwischen den Anordnungsobjekten des Ideallayouts ableitbar. Diese Größe verdeutlicht den logistischen Aufwand zwischen den Anordnungsobjekten im Funktionsschema.
Es resultiert das sogenannte Sankey-Diagramm. Darin sind die aus allen Produktfamilien hervorgehenden Transportintensitäten zwischen den Anordnungsobjekten zusammengefasst und in gerichteten, intensitätsproportional dicken Pfeilen veranschaulicht.
Schritt 3: Das Blocklayout
Durch die kapazitiven Betrachtungen beim Wertstromdesign erhält man den Platzbedarf der Ressourcen (vgl. Line-back-Prinzip). Damit sind alle für das Ideallayout erforderlichen Anordnungsobjekte in ihrer Dimension gegeben und können in ein Blocklayout überführt werden.
Schritt 4: Die Anordnungsoptimierung
Abschließend gilt es, die ideale Anordnung zu finden. Das ist aufgrund der Grundstruktur dieses Optimierungsproblems bereits für Layouts mit 20 Anordnungsobjekten nicht mehr in vertretbarer Zeit vollständig automatisiert lösbar. Darum nutzt man – wie oben angesprochen – Heuristiken und bestimmt zunächst
- die Anordnungspriorität der Blocklayoutobjekte und
- den Strukturtyp des Flusssystems (Netz oder Linie).
Das folgende Bild zeigt eine Visualisierung der Anordnungspriorität für das o. a. Blocklayout. Der Strukturtyp ist hierbei linear, die Anordnungsobjekte sind durch die verwendete Heuristik so eingefärbt, dass sich die ideale Anordnung durch Aufreihen der Anordnungsobjekte von Rot nach Grün ausprägt. Entlang dieser gedachten Linie sind die Blocklayoutobjekte nun möglichst dicht zu positionieren.
All dies erfolgt sinnvollerweise rechnergestützt unter Nutzung von Software, die eine grafische Darstellung der Anordnungspriorität sowie die Veränderung des Layouts unter Ermittlung des Transportaufwands in Echtzeit ermöglicht. Nur so können verschiedene Varianten effektiv erstellt und bewertet werden. Das Ideallayout ist das Ergebnis.
Die praktische Bedeutung des Ideallayouts
Es ist offensichtlich, dass diese Methodik nicht nur ideale Layouts hervorbringen kann, sondern auch im Bestand nutzbar ist. Dazu werden die Freiheitsgrade der Idealplanung mit Restriktionen belegt, wie z. B.
- Baukörper,
- gegebene Haupttransportwege,
- vorhandene Standorte schwerer Anlagentechnik,
- gegebene Technische Gebäudeausrüstung (TGA),
- nicht auflösbare organisationale Zwänge.
Viele dieser Restriktionen sind nur Experten des jeweiligen Fachbereichs transparent. Zudem können sie häufig nicht einfach formal beschrieben werden, so dass sie von einer Software zur Prioritätsbildung algorithmisch zu berücksichtigen wären. Insofern ist ein Wissenseintrag direkt in den Prozess der Layoutplanung notwendig.
Teamarbeit gilt darum als das Mittel der Wahl. Zeitgemäße Digitalisierungslösungen für die Layoutplanung unterstützen das gemeinsame Entwickeln und Optimieren von Layout-Ideen. Es muss dabei nicht immer gleich Virtuelle Realität (VR) oder AR sein. Denn ein Workshop mit Blocklayouts mit dem Ziel einer Optimierung größerer Fabrikstrukturen ist in 2D am ehesten zielführend. Zumal die Messgröße Transportaufwand und ihre Datengrundlage relativ grob sind und keinerlei immersionsfähige Modellbildung in der Detaillierung der virtuellen Realität erfordern.
Eine einfach zu handhabende digitale Lösung mit großformatigem Touchscreen wurde in der Forschung bereits zu Beginn dieses Jahrtausends als Zielsystem für Workshops zum Fabriklayout identifiziert. Mit heutiger Hardware ist so etwas nicht einmal mehr etwas technisch Außergewöhnliches. Man kann es einfach machen!
Fazit: Das Ideallayout als „Nordstern“
Wenngleich man in vielen praktischen Projekten der Layoutplanung im Bestand unterstellen mag, dass allein die Platzausnutzung Messgröße des Projekterfolgs sei, so werden genau diese Projekte i. d. R. nicht als vorzeigbar bewertet. Man ist sich bewusst, weit weg vom Ideallayout zu planen, aber derzeit geht es eben nicht anders. Ebendiese Vorgehensmuster führen zu sogenannten gewachsenen Fabrikstrukturen. Sie sind gefürchtet, weil ein Ausweg daraus häufig nur in radikaler Um- oder sogar Neuplanung gesehen wird. Die permanente Orientierung am Ideallayout öffnet hingegen eine Perspektive in Richtung kontinuierlicher Standortentwicklung. Das Ideallayout als „Nordstern“ ist das passende Bild dazu.
Ohne Zweifel jedoch hat das Ideallayout seine Bedeutung in der Neuplanung von Produktionsstandorten erlangt. Dort ermöglicht es den Entwurf der Fabrikstruktur als Groblayout, welche über die Planungsphasen hinweg sukzessive bis zum Feinlayout entwickelt wird (sh. a. VDI 5200 zur Fabrikplanung).
Verwandte Themen: