Groblayout und Feinlayout sind in der Fabrikplanung oft gehörte und meist auch intuitiv verwendete Begriffe. Fast jeder hat zu ihrer Bedeutung recht zügig ein Bild vor Augen. Grob steht für eher ungenau bzw. konzeptionell, während fein eher mit Ausgereiftheit, Genauigkeit und hoher Detaillierung in Verbindung gebracht wird. Und an der Stelle endet auch das intuitive Grundverständnis zum Sachverhalt. Sollte man mehr dazu wissen?
Nun, sicher ist es von Vorteil, die Aussagekraft eines Fabriklayouts richtig beurteilen zu können. Denn es ist keineswegs so, dass ein Groblayout lediglich die „unfertige“ Vorstufe des „richtigen“ Layouts darstellt. Und gar fatal ist es, sich erst mit dem Layout zu beschäftigen, wenn es als Feinlayout in weitgehend verständlicher, dreidimensionaler Form präsentiert wird. Dann nämlich ist es i. d. R. für viele Ideen zur Verbesserung längst zu spät. Viel zu viel Arbeit ist bis dahin bereits getan. Arbeit, die auf konzeptionellen Entscheidungen basiert und Arbeit, die unter wirtschaftlichen Aspekten nur einmal getan werden sollte. Aus diesem Grund wollen wir in diesem Artikel notwendige Perspektiven auf Grob- und Feinlayouts in der Fabrikplanung aufzeigen und ihre Nutzung erörtern. Es geht dabei um
- Reife (Level of Development)
- Granularität (Level of Detail)
- Hierarchie (Level of Information) und
- Materialfluss.
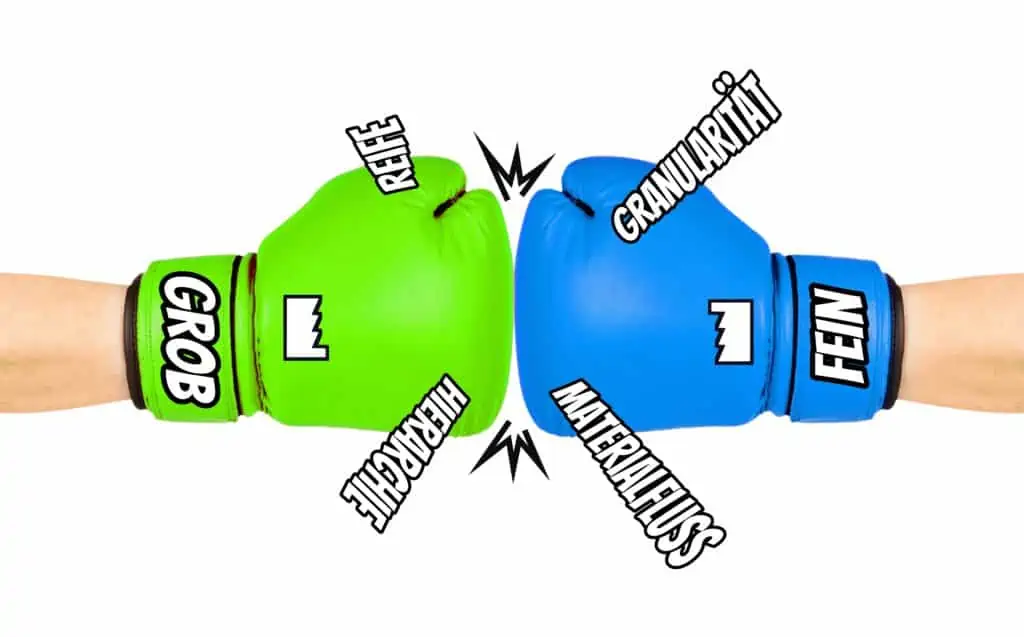
Perspektive „Reife“ (Level of Development)
Mit Reife soll der zeitliche Aspekt in der Layoutplanung beleuchtet werden. Dies ist auch der am einfachsten zugängliche. Denn neue Produktionslayouts entstehen in einem Prozess. Beginnend bei einer Zielplanung wird man sich in zeitlich aufeinanderfolgenden Phasen zur Realisierung des neuen Fabrik- oder Werkstattlayouts durcharbeiten. In der Literatur werden hierbei oft die Begriffe
- Ideallayout,
- Groblayout,
- Feinlayout
als zeitliche aufeinanderfolgende Reifegrade eines Layouts benannt. So ist beispielsweise in der im DACH-Raum weit verbreiteten Vorgehensweise nach VDI 5200 zur Fabrikplanung ein solcher Weg in den Phasen 3 und 4 beschrieben:
- Phase 3: Konzeptplanung; hier entsteht ein Groblayout zur Repräsentation des Fabrikkonzepts.
- Phase 4: Detailplanung; hier entsteht ein Feinlayout als Grundlage für die Realisierungsvorbereitung.
Reifephase des Groblayouts in der VDI 5200
Demnach wird in der Phase 3 (Konzeptplanung) ausgehend von einem idealen Funktionsschema zunächst ein Ideallayout erstellt, welches dann in Varianten mit dem Baukörperentwurf in Einklang zu bringen ist. Im abschließenden Schritt dieser Konzeptplanungsphase, der sog. Realplanung, soll ein Groblayout zusammen mit dem Gebäudevorentwurf das zu realisierende Fabrikkonzept beschreiben.
Reifephase des Feinlayouts in der VDI 5200
Das Feinlayout wird in Phase 4 (Detailplanung) der Vorgehensweise nach VDI-Richtlinie 5200 eingeordnet. Hierbei wird deutlich gemacht, dass ein Feinlayout i. d. S. bereits alles beinhalten muss, was für die notwendigen behördlichen Genehmigungsanträge und die Leistungsbeschreibungen erforderlich ist. Konkret bedeutet dies im Ergebnis z. B. für die Betriebsmittel, dass diese soweit detailliert sind,
- um zumindest Lastenhefte zu ihrer Ausschreibung daraus abzuleiten (sog. funktionale Leistungsbeschreibung).
- um gesetzliche Rahmenbedingungen zu identifizieren, nach denen ggf. behördliche Genehmigungen einzuholen sind (als Bsp. benennt die VDI 5200 das Bundes-Immissionsschutzgesetz – BImSchG).
Eine ähnliche Detaillierung wird in der VDI 5200 auch für weitere Systeme der Fabrik mit dem Feinlayout verbunden. Genannt seien bspw. Logistik, Arbeitsorganisation und Gebäude.
Perspektive „Granularität“ (Level of Detail)
Etwas schwieriger zu erfassen als die Reife ist die Granularität eines Layouts. Diese Perspektive ist auch mit den Begriffen „Auflösung“ oder „Detailliertheit“ gut zu veranschaulichen. Level of Detail (LoD) wird als Terminus technicus dazu verwendet. Eine Analogie liefert der Maßstab; wir haben dies auf unserer Themenseite zur Fabrikplanung am Beispiel „Weltatlas“ dargestellt.
Reife vs. Granularität
Reife und Granularität werden fälschlicherweise häufig gleich gesetzt. Dabei handelt es sich um die sprichwörtlichen zwei Seiten einer Medaille. Während die Reife eines Layouts mit dem Erkenntnisgewinn zu den Layoutobjekten steigt, kann die Granularität stets frei gewählt werden. So ist es beispielsweise möglich, ein Konzept für einen neuen Produktionsstandort bereits mit sehr detaillierten dreidimensionalen Betriebsmittelmodellen darzustellen.
Die Gefahr dabei liegt auf der Hand: Da man in der Konzeptphase das konkrete Betriebsmittel i. d. R. noch gar nicht so genau kennen wird, muss das im Layout verwendete Detailmodell folglich mehr oder weniger falsch sein. Falsch i. d. S. bedeutet, dass das später real genutzte Betriebsmittel in wesentlichen oder unwesentlichen Teilen eine andere Geometrie aufweisen wird. Nutzt man nun ein detailliertes Modell, kann niemand erkennen, welche Teile dieses Modells unrealistisch sind. Nur der Ersteller des Layouts weiß das. Damit wird ein Kommunikationsrisiko erzeugt: In den Köpfen der Betrachter entsteht ein u. U. falsches Bild von der Reife des Layouts.
Level of Detail
In der modernen digitalen Planungspraxis begegnet man diesem Risiko methodisch mit dem Konzept des sog. „Level of Detail (LoD)“. Vereinfacht gesehen bedeutet das, für ein und dasselbe Planungsobjekt mehrere geometrisch unterschiedlich detailreiche Varianten zu erstellen. Diese werden dann je nach Reife des Layouts bzw. der Layoutobjekte benutzt. Im Groblayout kommt ein Modell mit niedrigem LoD zum Einsatz, im Feinlayout ein entsprechend höher aufgelöstes.
Neben dem methodischen Effekt verbindet sich damit ein technischer Vorteil: Niedrig detaillierte Modelle erzeugen weniger Rechenlast für die Hardware, welche die Layouts darstellen muss. Damit bleibt mehr Rechenleistung verfügbar, die eine Planungssoftware dann zeitgleich zur Visualisierung des Layouts nutzen kann, z. B. für Auswertungs- oder Optimierungsberechnungen. Alternativ kann die Hardware dann mehr Modelle gleichzeitig darstellen, das digitale Planen ausgedehnter Layouts ist möglich.
Insgesamt sinken damit die Anforderungen an Hardware für die Layoutplanung. Teure „CAD-Hardware“ ist für Planungsaufgaben darum heute nicht mehr nötig. Dieser Aspekt sei hier betont. Denn in der Praxis hält sich immer noch die Auffassung, dass man für digitale Fabrikplanung in 3D auch hochperformante und damit kostenintensive Hardware benötigt.
Perspektive „Hierarchie“ (Level of Information)
Aus den bisherigen Betrachtungen, insbesondere zur Perspektive „Granularität“, ergibt sich nahezu zwangsläufig die Notwendigkeit, Layouts als hierarchische Systeme wahrzunehmen. Was bedeutet das?
- Zum Einen wäre da die Gliederung in Ebenen. Im einfachsten Fall ist das Groblayout die übergeordnete und das Feinlayout die untergeordnete Ebene.
- Zum Anderen kommt der System-Ansatz zum Tragen. Demnach besteht jedes System aus Elementen, die wiederum als Subsysteme des Systems aufzufassen sind. Auch hier kann im einfachsten Fall das Groblayout als System von Feinlayouts betrachtet werden.
In der Kombination dieser beiden Aspekte liegt der „Trick“. Sie erlaubt eine Vorgehensweise vom Groben zum Feinen und zurück in einem einzigen Modell. Erarbeitet man z. B. im Bestand ein Layout, so wird dieses ein Feinlayout sein – ein Abbild der realen Situation also. Dieses ist logischerweise bzgl. der „Reife“ nicht mehr weiter zu entwickeln, es ist ausgereift. Bzgl. der „Granularität“ kann es in folgend illustrierten Levels of Detail in Ebenen gegliedert werden.
Stellen sich nun Fragen zur Fabrikstruktur, nutzt man die Ebene Blocklayout. Das Verschieben oder das Verändern der Blöcke bzgl. ihrer Form ist unter Erhaltung ihres Flächenbedarfs vergleichsweise einfach ggü. dem alternativ denkbaren Verschieben und Einpassen der einzelnen detaillierten Layoutobjekte. Diese Alternative wäre i. Ü. bzgl. der Reife in der Strukturbetrachtung ja auch völlig unangemessen.
Beispiel Umzug mit Kapazitätserweiterung
Hier geht es um eher „grobe“ Dinge, wie z. B. dem generellen Platzbedarf aufgrund erwarteter Produktionssteigerungen. In dem Fall muss nicht nur einfach umgezogen werden, sondern es kommt ggf. neue/andere Technologie zum Einsatz oder eine Automatisierung in der Logistik wird dadurch rentabel. Das sind alles Dinge, die sich zwar im Platzbedarf grob berücksichtigen lassen, aber eben noch nicht ausgereift sind. Darum sind die Auswirkungen auf die Aufstellung der vorhandenen Ausrüstungen im Detaillierungsgrad des Feinlayouts nicht abzuschätzen. Ein Verschieben der vorhandenen Ausrüstungen in den favorisierten Bereich wäre also in dem Fall vergebene Mühe. Zudem werden Freiheitsgrade zu früh eingeengt und man „verrennt“ sich leicht im Detail.
Separieren von Groblayout und Feinlayout
Ein Feinlayout ist aufgrund seiner vielen Details mit deutlich mehr Informationen behaftet, als ein Groblayout. Hierzu beginnt sich der Begriff des Level of Information (LoI) zu etablieren. Das Feinlayout einer ganzen Fabrik wird daher nur selten von einer einzigen Person durchgängig erstellt werden können, Arbeitsteilung ist nötig und zudem sehr praktikabel.
Denn während man den Informationsgehalt eines Blocklayouts als Experte für Fabrikplanung relativ selbständig beherrschen kann, benötigt man für ein Feinlayout mit zahlreichen technischen und organisatorischen Details mehrere Experten. Es entstehen im Detail i. d. R. auch viel mehr Planungsvarianten. Daher ist es sinnvoll, das Blocklayout als geometrischen Rahmen für mehrere Feinlayouts zu nutzen. Die Feinlayouts selbst beinhalten dann jeweils nur einen Block dieses Rahmens, der von einem Expertenteam bearbeitet wird.
Beim Zusammensetzen der detailliert ausgearbeiteten Blöcke zu einem Feinlayout der gesamten Fabrik entsteht jedoch die Herausforderung, die Granularität des Feinlayouts erhalten zu müssen, ohne Grenzen der Hardware zu erreichen. Das ist insbesondere bei der Planung in 3D relevant. Ein technischer Ansatz dazu ist das Reduzieren der Objektmenge im Feinlayout der gesamten Fabrik durch (temporäres) Zusammenfassen aller Anordnungsobjekte des Feinlayouts eines Blockes zu einem geometrischen Objekt. Damit wird das LoI reduziert, das LoD bleibt. Für Layoutplanung genutzte Software sollte eine solche Arbeitsweise unterstützen, zumal dies unter der Perspektive „Materialfluss“ ebenfalls vorteilhaft ist.
Perspektive „Materialfluss“
Das einzige Problem, was die Erörterung in der Perspektive „Hierarchie“ offen lässt, ist die Abgrenzung der Objekte in der Hierarchie voneinander.
Welche Planungsobjekte eines Feinlayouts ergeben ein Blocklayout-Element?
Einen Lösungsansatz dazu bietet die Perspektive „Materialfluss“. Der Materialfluss bildet sog. Flusssysteme. Das sind diejenigen Elemente, die eine ununterbrochene Kette oder ein zusammenhängendes Netz aus Quellen und Senken ergeben. All diese Quellen und Senken sind Anordnungsobjekte in einen gemeinsamen Anordnungsraum. Ein Anordnungsraum darf dabei nur Objekte einer Hierarchieebene umfassen.
Beispiel zur Illustration von Grob- und Feinlayout in der Materialflussperspektive
Die folgende Illustration zeigt ein beabsichtigt einfach gehaltenes Layout aus zwei Hierarchieebenen (Blocklayout & Feinlayout). Die Anordnungsobjekte, die gemeinsam ein Flusssystem bilden, sind in ihrer jeweiligen Hierarchieebene farbig hervorgehoben.
- Das innere Flusssystem beschreibt den Fluss der Teile vom Eingangspuffer über die Maschine zum Ausgangspuffer. Dieses Flusssystem ist insoweit autark, dass es sich unabhängig von der Lage des gesamten Fertigungsplatzes in der Fabrik immer gleich ausprägt.
- Das äußere Flusssystem beschreibt den Fluss der Behälter in der Fabrik. Beteiligt sind die Lager und andere Fertigungsplätze. Auch dieses äußere Flusssystem ist autark, es prägt sich unabhängig von der inneren Struktur seiner Elemente immer gleich aus. D. h. z. B. ist es egal, wo die Eingangsstellplätze der Maschinen angeordnet sind, es muss immer die gleiche Menge an Behältern pro Zeiteinheit zum und vom jeweiligen Fertigungsplatz transportiert werden.
Beispiel Produktionsstandort
In einer Fabrik entstehen z. B. die beiden Anordnungsräume
- „Standort“ aus den Blocklayout-Objekten der Funktionsbereiche der Fabrik, also z. B. Eingangslager, Ausgangslager, Wareneingang, Warenausgang, Vorfertigung, Komponentenmontage, Endmontage u. vglb. in einem Groblayout.
- „Endmontage“ aus den Montagestationen der Endmontage, die ihr Material alle aus den Eingangspuffern und Kanban-Lagern der Endmontage (z. B. in Form eines PVB) beziehen und ihre Endprodukte in Ausgangspuffen dieses PVBs bereitstellen.
In diesem Beispiel sind die Ein- und Ausgangspuffer der Endmontage die Grenzelemente, welche die logistische Schnittstelle zum übergeordneten Flusssystem „Standort“ bilden. Alle Objekte innerhalb der Endmontage bilden zusammen ein autarkes Flusssystem (alle Stationen, Puffer, Kanban-Regale etc., also inkl. der Grenzelemente), ebenso alle Objekte des übergeordneten Flusssystems, die Blöcke des Anordnungsraumes „Standort“ also.
Nutzen der Hierarchie für die Optimierung der Fabrikstruktur
Die Elemente von Flusssystemen können mit Methoden der Fabrikplanung optimal zueinander angeordnet werden. Man spricht von einer Idealplanung, es entsteht ein sog. Ideallayout. Durch die Hierarchiebildung können mit diesen Verfahren sowohl ganze Fabriken als auch einzelne Produktionsbereiche als Anordnungsräume untersucht werden. Dies ermöglicht im Ergebnis eine ganzheitliche Optimierung der Fabrikstruktur unter weitgehender Reduktion von Komplexitätsproblemen.
Fazit: Grob- und Feinlayout im digitalen Fabrikmodell integrieren
Ziel eines digitalen Fabrikmodells sollte es sein, alle vorgenannten Perspektiven zu ermöglichen, nicht nur die von der Vorgehensweise in Projekten vorangetriebenen Ergebnisse. Denn während die intuitiv zugängliche Perspektive „Reife“ das erstmalige Entstehen eines Layouts fokussiert, also die sog. Neuplanung, resultieren die meisten Aufgaben der Layoutplanung aus Veränderungen im Bestand. Hier finden wir i. d. R. gewachsene Feinlayouts, aus denen gröbere Strukturen abgeleitet werden müssen, um konzeptionelle Planungsmethoden effektiv anwenden zu können. Vorteilhaft ist, wenn diese Strukturen bereits im Layout enthalten sind, also durchgängig eine hierarchische Perspektive beim Aufbau des Fabrikmodells umgesetzt wurde. Nur so können konzeptionelle Aspekte des Produktionslayouts untersucht werden, insbesondere die
- optimale Anordnung der Funktionsbereiche innerhalb des Produktionsstandortes und
- die Materialfluss- und Logistikstruktur.
Darüber hinaus ist es immer von Vorteil, eine zum Erkenntnisstand der Schritte in der Layoutplanung passende Granularität für die Layoutobjekte zu wählen. Denn die Granularität wird vom Betrachter eines Layouts intuitiv mit der Ausgereiftheit der Planung gleichgesetzt, was in der Kommunikation von Planungsständen leicht zu Missverständnissen führen kann.
Verwandte Themen:
Kein Problem, einfach für unsere Blog-News anmelden!