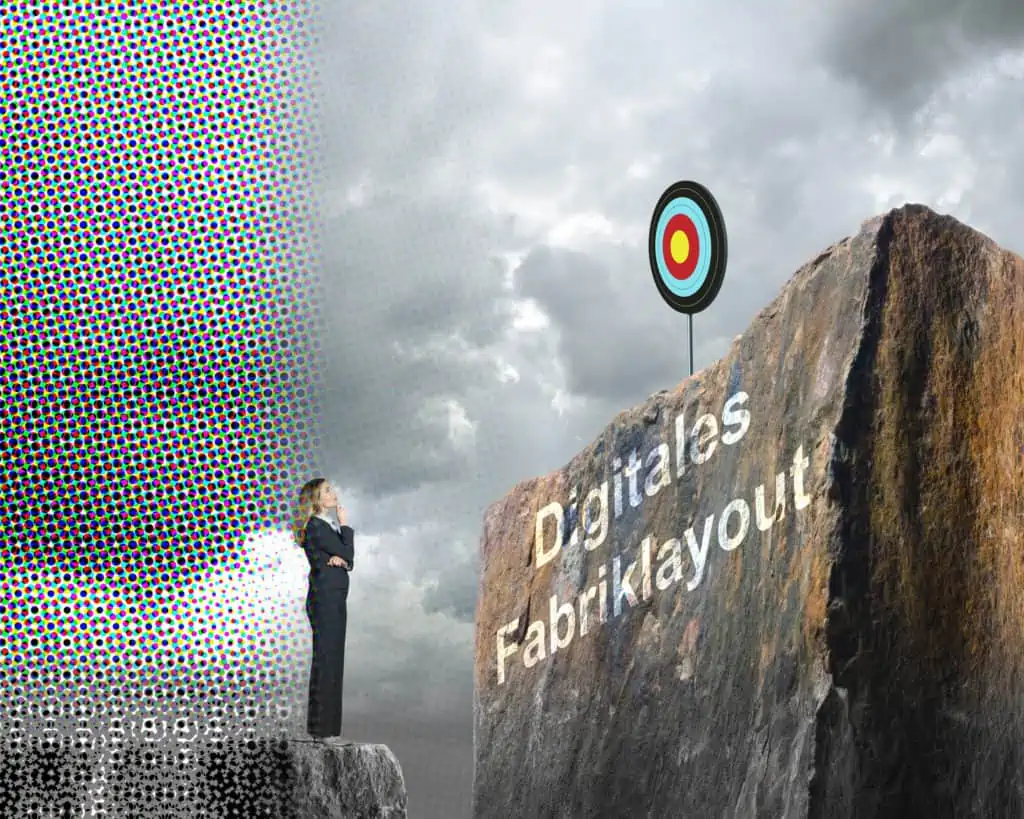
In diesem Artikel möchte ich das oft beworbene Thema Digitalisierung mittels Laser Scanning zur Bestandserfassung von Ausrüstung und Gebäuden aufgreifen und in den Kontext von Unternehmensgröße und Anwendungsfall in der Fabrikplanung setzen. Das ist auch gleichzeitig der Auftakt einer Artikelreihe zur Digitalisierung in der Fabrikplanung, die sich auch noch mit weiteren Erfassungsmethoden beschäftigen wird.
Grundsätzliche Fragen zum Stand der Technik und Anwendbarkeit
Vorab, es geht diesmal speziell um terrestrische Laser Scanner, eine Kategorie die häufig in der Planung von Produktionsstandorten Anwendung findet, neben den mobilen Scannern. Generell arbeiten terrestrische Laser Scanner von Leica oder FARO, mit ihrer Tripod-Aufstellung wesentlich genauer bei der 3D-Vermessung als z. B. ein mobiler Scanner der Firma NavVis. Sie sind aber dafür auch ca. zehnmal langsamer, wenn man sich die Scan-Fläche in m² pro Zeiteinheit anschaut. Schneller muss wiederum nicht besser sein und eigentlich ist das Scanning an sich kostenseitig schon fast egal geworden. Warum, das möchte ich im Artikel näher beleuchten.
Es soll vielmehr um kritische Fragen zur praktischen Anwendung in der Fabrikplanung gehen. Ich habe selbst seit 2007 Erfahrungen mit terrestrischen Laser Scannern in Forschung und Praxis gesammelt und auch die Entwicklung der Technologie bis heute miterlebt. Meine Erfahrungen sind aber nicht aus der klassischen Perspektive eines Vermessers gewachsen, sondern aus der Sicht eines Fabrikplaners, der erhobene 3D-Daten effektiv nutzen möchte. Ich schreibe hier auch vom am Markt erhältlichen, anwendbaren Stand der Technik. Aktuell arbeiten die Scanner von bekannten Herstellern z. B. noch nicht mit KI-Lösungen oder Deep Learning Ansätzen, um vielleicht Objekte direkt zu erkennen und live zu erzeugen. Sie scannen einfach alles was ihnen „vor den Laser kommt“, wenn sie sich drehen. Und so wird in diesem Kontext immer relativ schnell das Laser Scanning zur Digitalisierung von Gebäuden und Ausrüstung genannt. Gleich eins vorweg:
Laser Scanning ist (noch) nicht für jeden geeignet in der Fabrikplanung
Realistisch gesehen scheiden Unternehmen häufig schon allein bei einer Produktionsfläche von weniger als 2.000 m² für eine Digitalisierung mittels Laser Scanning aus. Die Anwendung käme der Floskel „mit Kanonen auf Spatzen schießen“ gleich. Oft reicht bei diesen Unternehmensgrößen die Bestandserfassung mit anderen Mitteln wie schneller Handvermessung oder Ausrüsterdaten mit groben Blocklayouts völlig aus. Selbst ein 3D-Modell kann hier schon überflüssig sein, wenn eingeschossig mit wenigen Maschinen, Regalen und Arbeitstischen in der Werkhalle geplant wird. Auf einigen hundert oder auch wenigen tausend Quadratmetern mit einem geringen Anspruch an die Genauigkeit, stehen Kosten und Nutzen hier aktuell häufig in keinem Verhältnis. Aber auch größere Unternehmen, die nicht in diese Kategorie fallen, tun sich erfahrungsgemäß schwer bei der Entscheidung ob Laser Scanning sinnvoll ist. Warum ist das so?
Ein Scan macht noch kein Planungsmodell oder digitalen Zwilling
Wenn man es auf den reinen Prozess der Erfassung eines Bestandes bezieht, bedeutet Digitalisierung mittels Laser Scanning erst mal nur Arbeit und ist neben der Zeit für Personal auch mit Kauf- und Mietkosten von Software und Hardware verbunden. Ich kann Stand heute mit einem terrestrischen Scanner wie dem Leica RTC 360 durchschnittlich 2.000-4.000 m² pro Tag innerhalb einer Fabrik erfassen. Das ist schon viel schneller als noch vor einigen Jahren, wo es nur 500-1.000 m² waren.
Habe ich nun eine 3D-Punktwolke vorliegen, kann ich mir diese in der von Herstellern bereitgestellten Software wie FARO Scene oder Leica Cyclone direkt anschauen. An diesem Punkt ist aus meiner Sicht der Nutzen für eine Layoutplanung aber noch relativ gering. Die anfangs gestellte Frage ist auch bewusst etwas provokativ, weil Laser Scanner Hersteller gern mit der Anwendung in der Fabrikplanung werben. Der Weg bis zum eigentlichen Ziel des Kunden wird dabei aber oft nicht ausreichend beleuchtet. Kunden stecken dann förmlich in einer Sackgasse, weil der Weg zum Fabriklayout (s. Bild oben) unklar ist. Aber schauen wir doch zunächst mal aus ganz praktischer Sicht, was hinter den Daten eines Laser Scanners steckt.
Punktwolken als Ergebnis der Digitalisierung mittels Laser Scanning
Heutige terrestrische Laser Scanner können um die 100 m weit messen und nehmen sage und schreibe bis zu 2 Millionen Punkte pro Sekunde auf. Neben der Punktposition im Raum wird auch ein RGB-Farbwert gespeichert. In farbigen Punktwolken lassen sich Objekte für uns oft besser wiedererkennen, aufgrund der Realitätsnähe. Scans in Graustufen können aber u. U. ein klareres Kontrastbild für die Rekonstruktion liefern. Ob ein Punkt mehr oder weniger genau aufgenommen wird, hängt auch von der Entfernung vom Austritt (Nodalpunkt) des Lasers zur jeweiligen Oberfläche ab. Hersteller geben das gern als Distanzabweichung an. Diese liegt heute ca. bei +/-1mm auf 10 m Entfernung.
Das ist aber nur die halbe Wahrheit. Entscheidend ist die 3D-Punktgenauigkeit (Abweichung in allen drei Achsen) und diese liegt beim Leica RTC 360 z. B. bei ca. 2 mm auf 10 m Entfernung wohlgemerkt. Danach nimmt diese immer weiter zu. Das betrifft übrigens alle Hersteller. Innerhalb eines Scans hat jeder Punkt dann eine fixe Position im Koordinatensystem des aktuellen Scans und es können viele, sehr viele Millionen Punkte in einer Datei bzw. einem Scan gespeichert sein. In einer Minute Scanzeit können so bei der oben genannten Scan-Rate mehr als 100 Mio Messpunkte entstehen.
Ausrüstung in Punktwolken wiedererkennen
Im Viewer kann man dann die Wolke aus Punkten, z. B. von einer Fabrikhalle oder einen Produktionsbereich ansehen und erkennt Objekte sofort wieder. Die steigende Ungenauigkeit auf Entfernung macht sich dann durch eine Art Welligkeit oder Rauschen auf eigentlich glatten Oberflächen bemerkbar. Die Scans und Objektumrisse werden quasi immer unschärfer. Je nach Auflösung und Abstand des Betrachters schwankt damit auch die visuelle Qualität im Viewer, abhängig davon wie der Punktabstand gerade ist. Letzterer wird in der Punktwolke mit steigender Entfernung immer größer. Praktisch heißt das dann, dass der Scanner ein weit entferntes Objekt nur noch mit deutlich weniger Punkten abbilden wird.
Nehmen wir als Beispiel einen 50 mm breiten Absperrpfosten den ich aus 20 m Entfernung scanne. Dann kann es sein, dass in der Horizontalen durch einen Punktabstand von 25 mm nur noch zwei Punkte zu sehen sind und ich das Objekt im Viewer vielleicht gar nicht mehr erkennen kann. Also muss ich näher ran, um die vom Scanner ausgehenden, auseinanderstrebenden Laserstrahlen wieder näher zusammenbringen zu können. Dann habe ich vielleicht 10 Punkte bei einem Punktabstand von 4 mm in der Horizontalen und kann den Absperrpfosten schon mal im Profil erkennen. Die Punktwolke können Sie sich als feinen Nebel aus Punkten ohne Linien und Flächen vorstellen. Glücklicherweise setzt unser Gehirn schnell ein Bild aus einer farbigen Wolke von Punkten zusammen. Die Punktwolke muss nur dicht genug sein (s. Bild oben). In der Praxis bedeutet das oft mehrere hundert Scans und viele Gigabyte an Daten um eine Fabrik zu erfassen.
Kein Problem, einfach für unsere Blog-News anmelden!
Der Weg zum Fabriklayout
Sie merken vielleicht schon an dieser Stelle, dass eine Punktwolke erst mal ein ziemlich ungeordneter Haufen an Daten ist. Fakt ist, der Punktwolke ist es egal ob wir nur eine einzelne Maschine, einen Behälter oder ein Wandelement betrachten wollen. Diesen gewünschten Objektbezug gibt es nicht, obwohl er für die Layoutplanung grundlegend ist. Es liegt nur eine definierte Menge an Punkten vor, mit all dem was der Scanner in einem Umlauf bzw. Scan sehen konnte oder eben auch nicht.
Ein Laser Scanner ist nur so gut wie sein Bediener
Das heißt eben auch, wenn jemand einen Gabelstapler vor einem Regal geparkt hat, dann wird eben dieser verdeckte Bereich auch nicht in der Punktwolke sichtbar sein. Das kann bei laufender Produktion auch während des Scans passieren. Genauso werden aber im Gegenzug unnütze Objekte, wie die Jacke, der Apfel und Kaffeebecher eines Mitarbeiters auf einer Werkbank mit aufgenommen.
Ein Laser kann weder durch ein Objekt schauen noch störende Objekte einfach herausfiltern (jedenfalls momentan noch nicht). Er sieht im Prinzip wie ein menschliches Auge nur das was nicht durch irgendwas verdeckt wird. Und was mache ich, wenn ich etwas nicht sehe? Ich ändere meine Position und stelle den Scanner immer wieder neu auf. Bei hoher Packungsdichte (stark zugestellten Fabrikbereichen) brauche ich deshalb sehr viele Scan-Positionen, um möglichst wenig Verschattung zu erreichen. Nichts ist nervenaufreibender, als sich im Büro später fragen zu müssen, wie ein Objekt aussieht, weil in der Punktwolke einfach Daten fehlen.
Tiefschwarze oder stark reflektierenden Flächen mögen die Scanner übrigens ebenfalls nicht. Es entstehen dann gern Löcher oder sogenannte Phasenverschiebungen und Streuungen mit Geisterpunkten an Stellen wo keine sein sollten.
Quick Wins durch Digitalisierung mittels Laser Scanning
Man spricht bei einer unbearbeiteten Punktwolke auch gern mal von einem sog. Störkantenmodell. Dieser Begriff zielt auch auf die Anwendung Kollisionsprüfung ab, wo man in die Punktwolke ein CAD-Modell lädt und die Machbarkeit der Aufstellung direkt innerhalb der Punktwolke prüft. Denn da lassen sich dann schon Überschneidungen zwischen einem 3D-Flächenmodell und der Punktwolke relativ schnell erkennen. Übrigens, Sie können in nahezu jeder Software zur Betrachtung von Punktwolken auch Punktabstände vermessen. Habe ich also ein aktuelles „3D-Foto“ meiner Fabrik, kann ich ohne viel Aufwand Abstände und Höhen in jedem erfassten Bereich messen. Dafür brauche ich auch keine besondere Aufbereitung der Scandaten oder das Herauslösen von Punktdaten. Was ich aber brauche, ist eine speziell auf Punktwolken optimierte Anzeige-Software (Viewer) die mit vielen Gigabyte an Scandaten umgehen kann und auch einen entsprechend starken Arbeitsrechner der über genügend Arbeitsspeicher verfügt.
Das Ziel des Laser Scanning kennen
Sei es drum, um diese Daten überhaupt für die Planung nutzbar zu machen, muss man sich erst mal seiner Zielanwendung bewusst sein. Die zuvor genannte Kollisionsprüfung oder einfache Punkt-zu-Punkt-Messung mal außen vor gelassen, da sie keine wirkliche Layoutplanung darstellt. Sowas wird in der Praxis eher punktuell für eine einzelne Anlage gemacht, wo man Kollisionsfreiheit in der Ausführungsplanung garantieren möchte. Deshalb folgend einige viele typischere Anwendungen in der Fabriklayoutplanung:
- maßstäblicher Hallengrundriss für IST-Layout
- maßstäbliche Höhen-Schnitte um bspw. TGA in verschiedenen Höhen zu berücksichtigen
- verschiebbare Ausrüstungsgegenstände für eine Anordnungsoptimierung
- Gebäudemodell zur Angleichung mit IST-Layoutdaten
Bei allen Anwendungsfällen entscheide ich prinzipiell ob 2D- oder 3D-Vektordaten oder sogar nur ein Bitmap (Pixelgrafik) erzeugt wird. Es wird aber schnell klar, dass die Rohdaten (wilder Punktehaufen) vom Scanner für diese Anwendungsfälle erst einmal unbrauchbar sind. Übrigens ist eine 2D-Rekonstruktion wesentlicher kostenschonender als in 3D, aber eben auch mit wesentlich weniger Informationsgehalt verbunden.
Sind Sie jetzt noch dabei? Oder haben Sie schon an dieser Stelle für sich entschieden das Thema wieder abzuhaken? Wir kommen noch zu weiteren nützlichen Anwendungen, versprochen.
Die Hürde der Transformation – Von Punkten zu Planungsobjekten
Wir gehen mal davon aus, dass Sie bereits die Einzelscans zu einem Gesamtmodell zusammengesetzt vorliegen haben (sog. Registrierung). Und die Punktwolke wurde auch schon von Störpunkten befreit (weitere Arbeitsschritte in Vorbereitung). Wohlgemerkt wir sprechen immer noch von Punkten, keine Flächen, geometrische Primitive oder CAD-Modelle und von Datenmengen die schnell viele Gigabyte groß sein können.
Dann beginnt jetzt das was gern von Anbietern auch mal verschwiegen wird, die Aufbereitung oder Rekonstruktion zur Überführung in wirklich nutzbare Daten. Denn wenn Sie nicht nur Ihre Fabrik in 3D dokumentieren, sondern auch planen wollen, muss noch Einiges mit den Scandaten geschehen. Im zweiten Teil soll es demnächst um konkrete Anwendungsfälle, eingesetzte Software und Beispiele aus der Praxis gehen. Warum sind die wirklichen Kostentreiber der Bestandsaufnahme hier angesiedelt und gibt es Alternativen?
hier geht’s zum zweiten Teil dieser Blogartikelreihe: