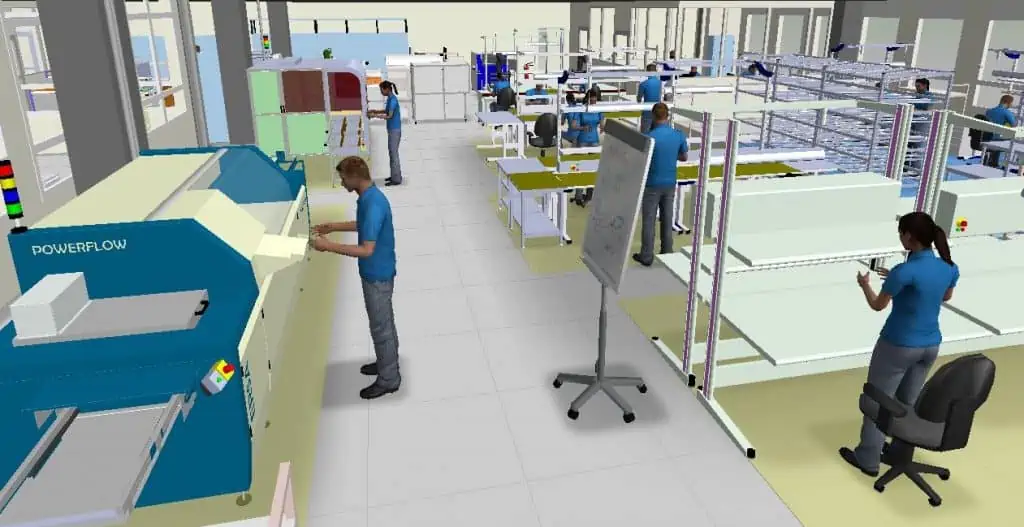
Die Sorin S.p.A ist Hersteller von Medizintechnik mit Fertigungsstandorten in Kanada, USA, Brasilien, Frankreich, Italien und Deutschland. In München werden bei der Sorin Group Deutschland GmbH Herz-Lungen-Maschinen, Autotransfusionssysteme und Hypothermiegeräte entwickelt und gefertigt.
Aufgrund steigender Stückzahlen, neuer Produkte und einer erhöhten Fertigungstiefe war eine grundlegende Reorganisation der Fabrik in München nötig. Die Layoutplanung sämtlicher Produktionsbereiche erfolgte bis dato auf Basis einfacher 2D-Modelle, die ausgedruckt, ausgeschnitten und auf einem ebenfalls ausgedruckten Layout so lange manuell verschoben wurden, bis ein subjektiv optimales Layout erreicht wurde.
Nutzen durch den Einsatz von visTABLE®
- Deutlich verringerter Planungsaufwand aufgrund intuitiver Bedienung der visTable®touch Software
- Einfacher und schneller Vergleich unterschiedlicher Layout-Alternativen
- Valide Ergebnisse aufgrund Materialflusssimulation
- Erhöhte Akzeptanz der Layout-Neuplanung bei Mitarbeitern und Werkern aufgrund der anschaulichen 3D-Visualisierung
Es galt, den zwar einfachen, aber ineffizienten und ungenauen Planungsprozess bei Layoutänderungen grundlegend zu optimieren.
Vor allem die wenig exakten Ergebnisse, die keine validen Zahlengrundlagen hatten, führten zu langen Diskussionen und wurden zunehmend zum Problem. Stephan Süß, verantwortlich für Lean Manufacturing, suchte 2012 nach einer geeigneten Softwarelösung. Ein erster Test von visTABLE® war aufgrund der einfachen Bedienung der Software sehr überzeugend. Da weder Nutzen noch potenzieller Aufwand für die digitale Planung bekannt waren, entschied man sich, zunächst vom visTABLE®-Pilotpaket Gebrauch zu machen.
Entwurf für ein Soll-Layout
Der für das Pilotprojekt ausgewählte Produktionsbereich hat eine Fläche von ca. 750 m² und umfasst mehrere Anlagen zur Platinenfertigung sowie zahlreiche Handarbeitsplätze für Montagetätigkeiten. Florian Gernbeck, verantwortlich für die Projekt-durchführung, erstellte zunächst mithilfe von Solid-Works eine dreidimensionale Abbildung sämtlichen relevanten Inventars und der Gebäudehülle. Erfreulich war die Bereitschaft vieler Anlagenlieferanten, Konstruktionsdaten der vorhandenen Anlagen für die Aufbereitung und die anschließende Verwendung freizugeben. Sämtliche Objekte wurden im Anschluss mit dem visTABLE®-Objektmanager importiert. Für den Aufbau des Layouts und der Materialflüsse waren 50 Arbeitsstunden nötig.
Deutlich reduzierter Planungsaufwand
Nachdem das vorhandene Layout mit Materialflüssen abgebildet worden war, wurde aus diesem Modell ein erster Entwurf für ein Soll-Layout entwickelt. Dieses diente als Diskussionsgrundlage für die ge-meinsame Planungssitzung.
Schon in der ersten Runde konnte ein neues Layout nach Lean-Kriterien verabschiedet werden, was in der Vergangenheit nicht denkbar gewesen wäre. Möglich wurde das beschleunigte Planen, weil visTABLE® neben Objekten und Materialflüssen überzeugende Funktionen zur Layoutbewertung be-inhaltet. Das Vorgehen ist so für alle Beteiligten transparent und nachvollziehbar und führt zu einer deutlich erhöhten Akzeptanz bei Planern, Entschei-dungsträgern und Werkern. Aufgrund der Erkenntnisse entschied man sich, die Software visTABLE® für die ganzheitliche Fabrikplanung einzu-setzen.