Close to the Digital Twin and yet past it – heavyweight 3D CAD data
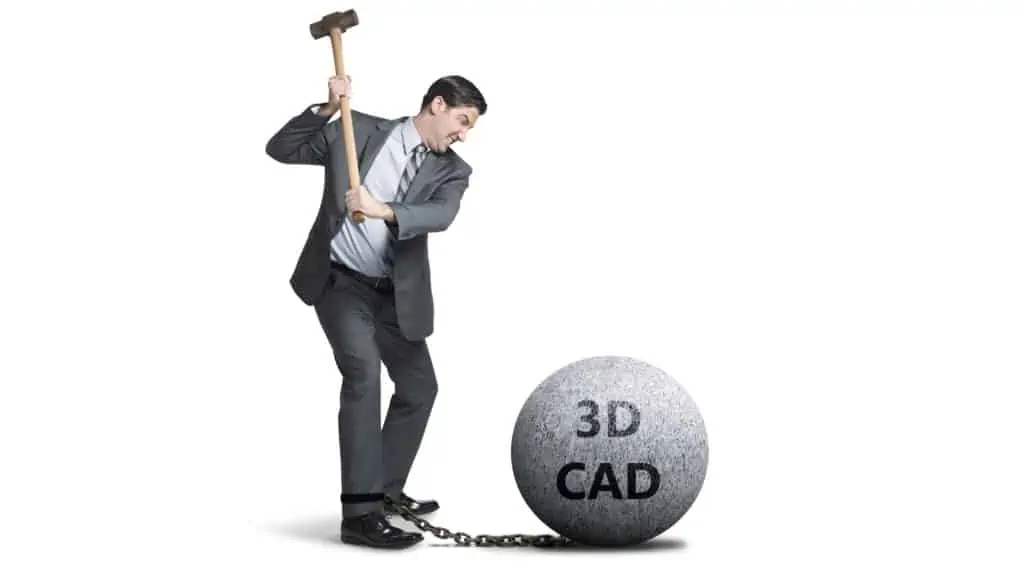
Are you also sometimes annoyed in the project, if you have to load again a too complex 3D model as STEP, DWG, or OBJ into your layout? You already know that 500 MByte will not make your factory layout leaner. But with a simple block representation, you will not attract anyone in the current planning phase. It is also too late to hire a service provider and the budget for this has already been used up. A dilemma of time pressure and communication problems arises. Is there a way to get this model to 5 MByte by the deadline?
This is exactly the topic of this article. What are practical solutions to radically and above all automatically simplify 3D data for layout planning? For more information on why this is so important, see also the blog article on handling CAD data. The solutions presented here are selected examples and do not claim to be complete. Contents will be updated again and again in the future.
Radically simple through remeshing instead of reduction
With so-called Remesh or Shrinkwrap methods, it is actually possible to get the large data volumes of 3D CAD models automatically down to 1% or even 0.1% of the original data volume. The time saving and very strong reduction is however also bought with cutbacks in the model quality. You should know this in advance. But this is certainly still better than not having a 3D model at hand at all, isn’t it?
In simple terms, remeshing is the creation of a completely new surface mesh over a very complex 3D model. The original geometry serves only as a reference for a highly simplified envelope model. Imaginable as a tarpaulin over the boat in the picture above or a shrink wrap around vegetables in the fish department. Ideally, small details, such as holes and screws, and even internal parts of a CAD model of factory equipment disappear.
Example of automatic simplification of 3D CAD assembly workstation
In practice, this means that a true remesh approach can often remove up to 99% and sometimes up to 99.9% of data. Nevertheless, the external appearance is largely preserved in the generated envelope model of equipment. The following is an example of a complex assembly table that was greatly simplified by remeshing within 1-2 minutes:
In principle, the open and complex structure represents the most difficult case. Especially manual simplification is often very time-consuming because there are hardly any internal parts that can be easily removed.
The footprint of the equipment is very well preserved. Significant reductions in the display quality can be seen with increasing reduction. The reduction of the number of geometric objects from 350 to one geometry is also remarkable. The model receives the color information via the automatically generated texture atlas:
Ultimately, this results in an enormous acceleration of the 3D representation in your factory layout. Feels can range from “barely manageable” to “this runs super smooth”. In practice, this possibility can possibly decide the success of a planning workshop or a project.
Other options for automatic simplification of 3D models – polygon cruncher
Besides the remesh solution described above, common reducers only try to adjust every single object (geometry) in the assembly and thus simplify it. Holes, screws, even internal and invisible parts often remain as barely recognizable details if the software does not filter them. In principle, therefore, all individual parts are retained. Complex CAD data sets can contain several 10,000 parts.
With this method, you can then often achieve only 50% to 90% smaller models, whereby even here clearly visible representation errors can occur. Well-known tools of the conventional, also edge-based method, are among others
- SAP Visual Enterprise Author (formerly Deep Exploration)
- VRSQUARE Meshmatic
- Mootools Polygon Cruncher
- Okino NuGraf
- Atangeo
- 3ds Max ProOptimizer (standard plugin)
This simplification option is available in almost every authoring system that works with polygons. Also, CAD systems often have the option to select a level of detail or resolution when exporting CAD datasets. However, these only help us to a limited extent with highly complex product data, because there is still too much data remaining in the model. 10% of one million surfaces are still 100,000 surfaces and can become a problem in a complex factory layout if used frequently.
3D-CAD optimization determined by application
By the way, this is not to say that these solutions are fundamentally bad. Remesh solutions also offer this method in addition. They have a raison d’être above all when it comes to simplifying complexly networked, organically shaped individual geometries or in the technical field when the component structure of an assembly must still be preserved. However, these requirements have no meaning when generating a very simple envelope model for the conceptual design of a factory.
What Remesh software is available for automatically simplification of 3D models?
Basically, remesh solutions can be divided into two camps. There is software from the entertainment industry that was primarily developed for optimized 3D assets in video games. In this context, the simplified models are also referred to as proxy LOD. These are automatically inserted in games at greater distances as “substitute geometry” in order to increase the 3D performance or frame rate.
These software solutions are then, in addition to standalone versions, also often already integrated into 3D engines such as Unity or Unreal. These include:
Then there are solutions that are more technical in nature, originating from the multi-CAD environment or generally targeting 3D content from all sorts of areas, such as:
All in all, it can be said that there are already very mature and easy-to-use solutions. Especially in the area of online services for remeshing the development is still in progress. Meshlab should also be mentioned in passing as a free solution with an experimental character in this area.
What is important in a good remesh solution for concept planning?
In summary, it is mainly the following points:
- Preservation of model boundaries or footprint in x, y and z for high planning accuracy.
- robustness and speed – can handle very large data sets (500 MByte and more) very well
- strong simplification up to 99% and more – removes any internal details, components that are hardly or not visible, as well as typical CAD features like holes and curves, reduces homogeneously with defined resolution to one or only a handful of single objects
- UV Texture Atlas – can create an image (texture) based on the original detailed model, simulating details in the simplified model – preserves the exterior appearance of the original as good as possible
- ease of use – editing at the touch of a button, simple configuration of a few parameters
- format diversity – can read in many different file formats and also export them again
- local calculation possible – independent of untested cloud services to protect sensitive data
- reasonable price – depends on the frequency of use and the result
In principle, only solutions from the entertainment industry meet most of the criteria. Simplygon, for example, generates respectable and very highly optimized models in a very short time. Typical input formats from the CAD area like STEP or IGES are missing here, however. A prior conversion to Wavefront OBJ, for example, is therefore necessary for the tool to work.
Online service portals as a flexible solution?
Solutions such as DGG RapicCompact and Meshmatic that function like online service portals are certainly interesting. There, you can upload files for processing and often download the result after just a few minutes. Of course, this raises data protection issues. Companies don’t like to store data on a third-party cloud. This is where DGG or Simplygon offer local solutions. This means that 3D CAD data does not leave your computer. For example, only the frequency of use is transmitted to the provider for billing purposes. In any case, you should clarify this question of data handling with the provider in advance so that you do not experience any surprises with sensitive data.
Complex and individually adaptable optimization solutions
The 3D Evolution Simplifier solution from Coretechnologie, on the other hand, is already being used in larger companies as a standard solution for CAD data reduction “overnight”. This is comparatively complex with numerous configuration options. It, therefore, differs from the usually more simply structured solutions in the entertainment sector. Application areas for this are, for example, product data management, where lean 3D data sets are required for joint viewing in a team. So the requirements are very similar to those of participatory factory planning with many stakeholders. Together with Simplygon, it is one of the more high-priced solutions that require regular use. A plus point here is the import of well-known CAD formats such as CATIA, NX, JT, Inventor, STEP, Creo, SOLIDWORKS.
Conclusion
Especially for the concept planning of a factory, the proxy LOD or simple replacement geometries can help to get the complexity of CAD product data under control. For this, it is sufficient to get a single strongly simplified geometry (envelope model) with largely preserved color information (texture atlas) and footprint as a result.
It is interesting that especially solutions like Simplygon from the entertainment sector master this task very well, but on the other hand do not support the typical CAD formats. The more technically oriented solutions are sometimes too complex to adequately cover the rather simple use case, but often offer the required CAD interfaces (3D Evolution Simplifier, Meshmatic). Not to be forgotten are also shrinkwrap functions in CAD systems, which are intended for the generation of simplified meshes for simulation applications, for example. While these do not emphasize the preservation of color information, they can also greatly reduce complexity.
Between block layout and high-quality design model
If you’re thinking in terms of final presentations or workshops in VR, a Remesh solution may not deliver the quality you want. This is because the level of detail of a proxy LOD is best suited for viewing from greater distances. In that case, you might want to plan on working with a professional service provider in time after all. They can transform your CAD data into high-quality, lean 3D models, albeit with significantly more effort.
No problem, simply subscribe to our Blog-News!