Any manager would no doubt agree that optimized space utilization in production and logistics areas is a key goal of factory planning. After all, space is a limited resource. Where optimization is on the agenda, value-adding and waste are shifted into the focus of attention. But how can these factors be measured and evaluated in the context of planning floor space utilization?

When is space utilization optimal?
“Optimal” is a frequently used adjective when formulating objectives to improve productivity and efficiency, also in floor space utilization. The optimum typically is the minimum area occupancy to realize the production task. In other words, as much value-adding potential as possible must be accommodated per unit of floor space. Some metrics offer orientation: In the retail trade, for example, we speak about surface area productivity, which means the turnover generated per square foot.
In manufacturing and assembly, categories and metrics of lean production are customary. Examples which can be mentioned are value-adding, value-supporting, and waste. In the case of a machining group, the workspaces of the machines can be declared value-adding areas. Handling or staging areas, on the other hand, are value-supporting. Areas for the storage of tools and fixtures belong to the same category. The remainder is waste.
If these classifications are extrapolated for a whole factory, the result is a very small space utilized for value-adding. Floor space utilization planning must also observe a diversity of standards, guidelines, and laws. Aspects covered by space use metrics or space optimization include escape route widths, safety clearances, and circulation or functional areas. None of this fits into any of the value categories and must thus be considered waste.
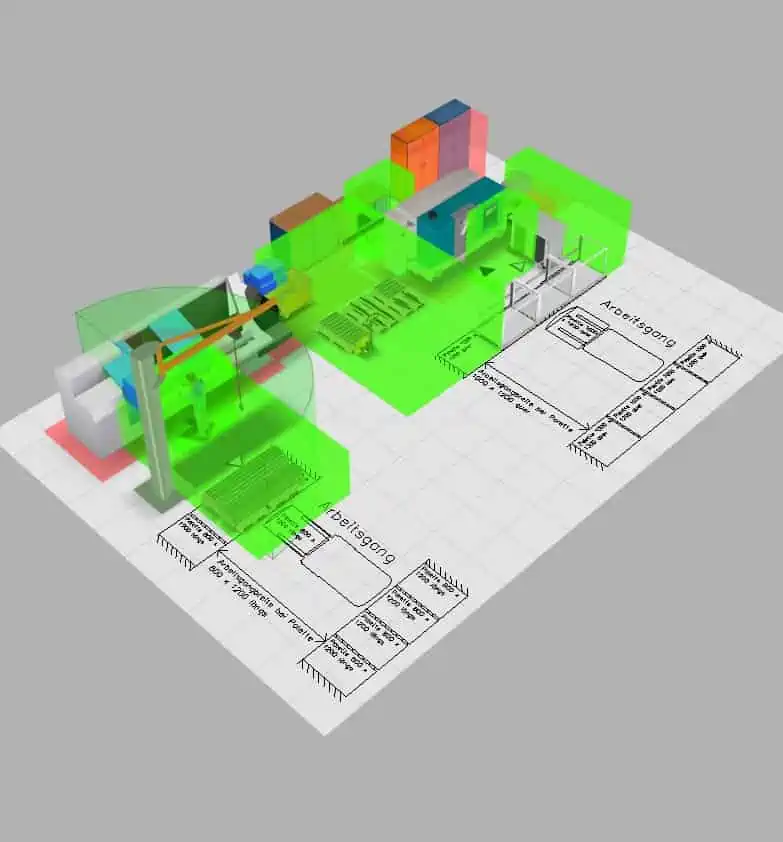
Another aspect of any space utilization metric is that different areas may overlap. In an assembly center, for example, materials may be supplied directly into the extended reaching space above the workplace. In the top view, the value-adding and value-supporting areas then overlap. This measuring effect is always to be observed where equipment is used at several levels. A transport system for example suspended from the hall ceiling is especially space-saving. On the other hand, it is technically more complex and less flexible than floor conveyors.
These examples illustrate the multitude of factors to consider when describing an optimum utilization of floor space. And that is probably the main reason why there are so few benchmarks for floor space utilization in production. Consequently, planners follow the simple rule to utilize as little floor space as possible.
Approach to floor space planning
Generally speaking, the best solution to a floor space planning problem will thus lie in a comparison of different variants for the facility arrangement. An area balance supplies the necessary indicators for space usage. It measures the facilities’ occupancy of floor space divided into area categories and their corresponding proportions of the total floor space.
It must be noted that measuring space utilization with area balances generally pursues different knowledge goals for a site. It is thus useful to specify separate measurement levels from workplace to factory site, each with its own area categories. Hierarchy levels within the factory can provide orientation, for example, workplaces, departments, halls, or premises. This enables areas to be categorized according to aspects of value-adding at the workplace level while maintaining functional classifications at the site level.
Software support for space utilization
Improving the use of space is only one of many layout improvement measures. But the metric of an area balance is more than a simple aggregation of spatial measurements. It can become a quite complex calculation. After all, production and assembly areas are often not simple rectangles. All manner of polygons is encountered, for example, L-shapes. Possible overlaps of different area categories also play an important role. In other words, calculation metrics can quickly evolve into an exercise for spreadsheet freaks.
Beyond space utilization, layout planning has to provide other outputs. To improve planning productivity, it must be possible to quickly try out and evaluate new layout ideas. It is thus only logical to expect factory planning software not only to include a metric for floor space occupancy but also to offer usage as simply as possible. In this context, the answers to the following questions can provide the necessary orientation:
- Is there an explicit software function for space utilization (area balance)?
- How complex is the elaboration of an area balance, and could it even be done automatically in real-time?
- Does the software itself offer relevant templates?
- Can area categories be defined or added by the user?
- Are the metrics transparent regarding the overlapping of areas?
- Is it possible to influence the range of the evaluation (balance domains)?
- Is there an output function to export the area balance?
- Does the software offer an input function to import tabular space utilization data (e.g. from Excel)?
You can assess how useful such features are in floor space planning by testing the visTABLE® trial version: