Relocation to 143,000 m² of new factory space while at the same time implementing an optimum product flow
MainChange is probably one of the most significant innovation projects ever undertaken by SAMSON AG. The first thoughts were already brought to paper in 2021 and served as the basis for a feasibility study. The trigger was a desire for further growth, which was no longer possible at the present manufacturing site in Frankfurt am Main. And so, as expressed by the deliberately ambiguous project name, the company is about to implement the “most important transformation” in its history.
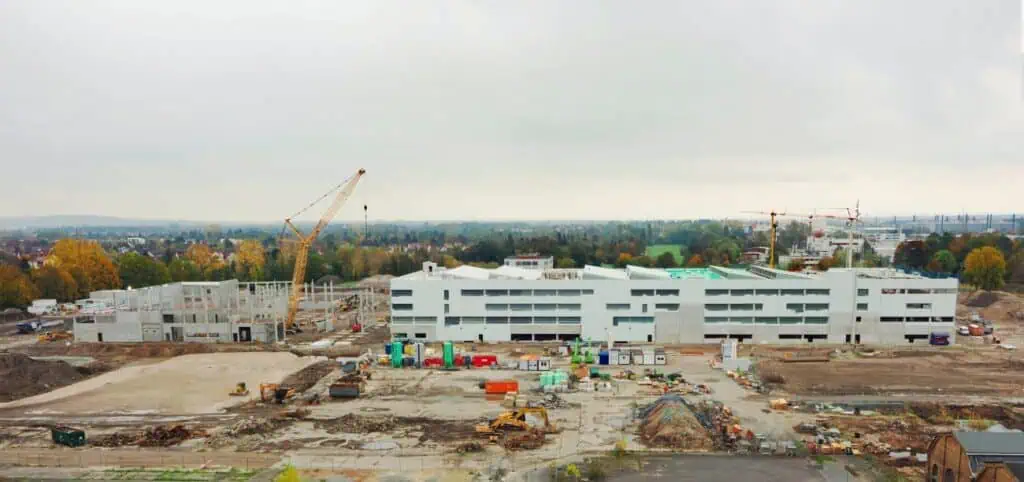
Relocation of the company headquarters and its 2,000 employees to Offenbach on the opposite side of the Main River is an enormous challenge, but at the same time a great opportunity. The currently fragmented facility will become much more concentrated at the new 143,000 m² site, enabling internal factory logistics to be organized significantly more efficiently.
The move is to be completed by the end of 2026. To ensure that this schedule can be met, the company has turned to the software package visTABLE® for factory planning.
“We have accelerated our planning enormously thanks to visTABLE®,” says Dirk Dammköhler, production engineer at SAMSON AG and assembly subproject manager within the MainChange project.
In the past, planning was done using Microsoft Visio. But at the latest when work began on construction of a whole new factory, that approach was no longer able to meet the expectations of the SAMSON AG factory planners.
What does SAMSON AG produce?
SAMSON AG is a specialist supplier of smart control valve technologies with manufacturing headquarters in Germany and an active presence in more than 80 countries worldwide. Its products come to the fore wherever industry is dependent on controlled flows of oils, gases, vapors or chemical substances. The high in-house manufacturing ratio of more than 86% allows solutions to be tailored individually to the customer’s applications. Components with dimensions of up to several meters require corresponding storage space and are not easy to handle. Accordingly, planners at SAMSON AG attached particular importance to optimization of the principal logistics routes in the factory.
Internal transport drastically reduced
In the current, four-floor production building that accommodates the control valve assembly, materials must still be transported between the four levels by elevator. The planners have resolved this bottleneck for the future by bringing material transports and associated production processes together on one full floor.
“Everything must be in constant flow, with the shortest possible distances and across all departments. One way to achieve that is layout optimization in visTABLE®,” says Dirk Dammköhler.
The main logistics axes allow materials to be transported quickly into and back out of the building. With a width of 4.50 m, they are also designed to support the bidirectional circulation of driverless automated guided vehicles, as can be seen in the illustration below.
Within the individual production areas, too, particular attention is paid to smooth product and component flows. After all, many production jobs require workpieces to be transported between multiple workplaces.
Through material flow optimization using visTABLE®, the transport distances for the various components of a control valve could be reduced significantly. Dirk Dammköhler was delighted with the outcome: “visTABLE® really helped us in this respect.”
Flexible team planning in the assembly and production areas
But how has the team at SAMSON AG arrived at a final layout? “In practice, that is actually a continuous process,” says Dirk Dammköhler, himself a key user and at the same time subproject manager for the assembly area. An initial layout was already planned in visTABLE® at the very beginning, taking into account relevant lean production principles and other process considerations. Five members of staff belong to the core team, and ten project contributors are using visTABLE® in the company. The assembly and production areas are here working relatively independently on their respective layouts.
Regular cross-departmental workshops are held to coordinate progress. visTABLE® permits live changes to the layout with immediate performance indicator feedback during these meetings. This also means that the head of assembly and other SAMSON AG decision-makers can base their further discussions on the actual impact of a changed product flow.
The team also uses visTABLE® – together with the maintenance department – to optimize planning of the building services installations, and here specifically to ensure the required media supplies to individual workplaces or whole production segments.
Site in Offenbach am Main – ideally prepared for the future
“We are building a factory for the next generations,” says Dirk Dammköhler. The goal of SAMSON AG is to position the company for a secure long-term future. Flexibility is one of the most important criteria for the new site. The individual segments of the production areas, for example, have been planned with a view to possible reassignment at a later date. Each segment measures approx. 6 x 13 m and offers a certain degree of modularity to enable fast response to changed market demands.
In this connection, SAMSON AG is also taking advantage of the area balance functionality in visTABLE®. “Here and there, we have uncovered additional potential and have defined our own area type ‘growth area’ to label such spaces,” says Dirk Dammköhler.
Words of thanks
We would like to thank SAMSON AG for sharing its experiences with visTABLE® and wish the company continued success for the development of its new headquarters in Offenbach!