The term “simulation” is on many people’s lips – but what does it actually mean for practical use in industrial companies? How can a planner follow the “First Time Right” approach without getting lost in over-engineering? How is the visTABLE® planning software to be classified? You can find a summary as a table at the end of the article.
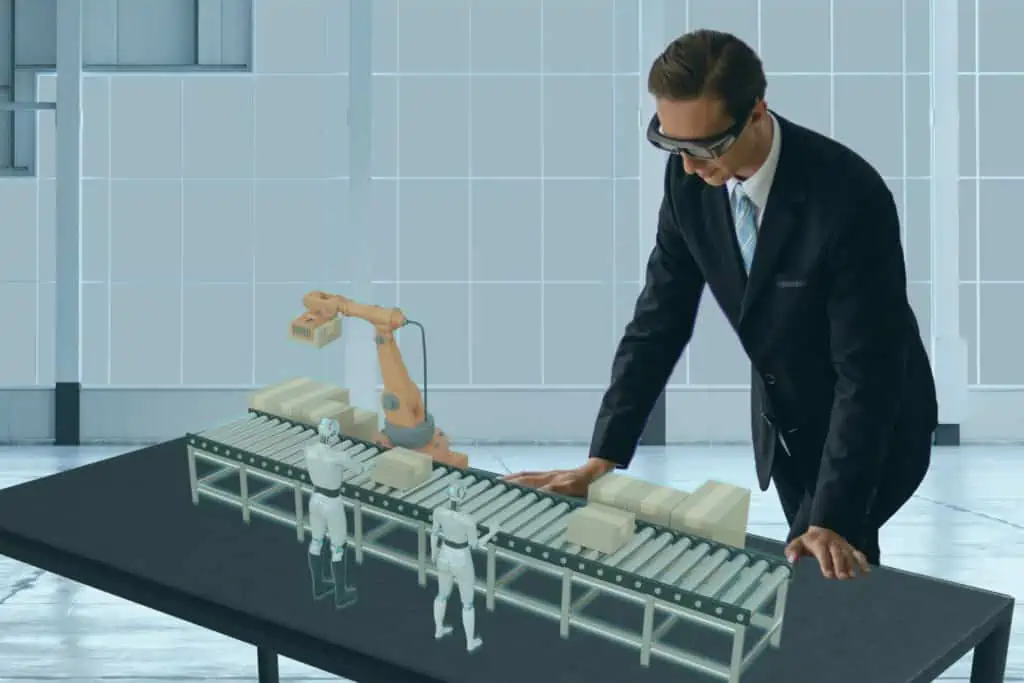
What are the advantages of simulation?
With the help of simulations, what-if scenarios can be played through and processes can be tested and visualized before they even exist. In this way, various manufacturing processes and the resources required for them can be parameterized and evaluated already in the planning phase. This enables a high-quality and efficient design of plants and processes. A good simulation solution is also characterized by the fact that its results are presented transparently, clearly, and understandably even for non-experts.
What insights are gained by the simulation?
In discussions with customers and users, we repeatedly discover that there are many different ideas about what a simulation actually is. They range from a 3D representation to complex process simulation. Here it is first of all necessary to compare the expectations of this planning instrument. It is also important – at least for factory and material flow planning – to have sufficient process knowledge. For the success of simulation-based planning, close cooperation between IT, planners, and production experts is therefore essential.
What IT infrastructure is required?
No special hardware is required for the use of simulation solutions. Rather, it is important to have the necessary know-how for the targeted use of simulations. In addition, data acquisition is an important issue, which is different for every customer. If no or insufficient operating data is available, we can help ourselves with simplified models, e.g. static calculations.
Excerpt from the exchange of words “Simulation for planning and optimization of assembly systems” in the Competence Atlas Assembly – collaborative and versatile
A smart alternative
Process simulations are complex and cost-intensive. They require a digital model of the production area to be illuminated as well as an extensive, well-founded database. The necessary personnel capacities should also not be underestimated, since technical specialists are often very well utilized
CAD systems, on the other hand, are less expensive and often already available in the company. They can be used to map the geometric model of a factory. However, there is a lack of planning support for system-immanent processes (e.g. material and goods flows). The planning results are therefore “only” geometrically valid.
Direct comparison of planning software and material flow simulation
Planning software | Material flow simulation |
Use case: structure and layout planning | Use case: detailed planning |
• Concept planning and variant investigation | • Bottleneck analyses |
• Placing objects on the layout | • Utilization of machines |
• Optimization of the transport costs | • Dimensioning of buffers |
• Determination of area keyfigures | • Investigation of control strategies |
• Derivation of equipment lists | • Investigation of dynamic parameters |
• Machine cadastre | • Examination of random variables |
Data basis | Data Basis |
• Product data, process data, resource data | • Product data, process data, resource data |
• Time reference of the data basis month or year | • Time reference of the data basis second or minute |
• Derivation of the database can be realized at short notice | • Derivation of the data basis usually greater effort |
• Data volume manageable | • Data volume usually larger and more detailed |
Model creation effort | Model creation effort |
• A few hours or days | • Days to weeks |
• No CAD or programming knowledge required | • Programming knowledge required |
Result | Result |
• Achieve 80 % effects with 20 % of the effort | • Achieve 20% effects with 80% of the effort |
• Fast results through simple operation | • Detailed planning of complex interrelationships |
• Use by several users | • Use only by specialists |
Variety of actors | Selected experts |
• Factory planner | • Simulation expert |
• Lean manager | • Programmer |
• Logistics planner | |
• Work planner | |
• Occupational safety | |
• Master | |
• … |
The visTABLE® planning software for example combines concepts from both worlds. The geometric model is enriched with selected motion data. However, no endless columns of figures need to be entered. Initial results can be achieved with just a handful of data. Especially in the early phases, this minimized method avoids planning errors, which can have very costly consequences later on. Try it out yourself!