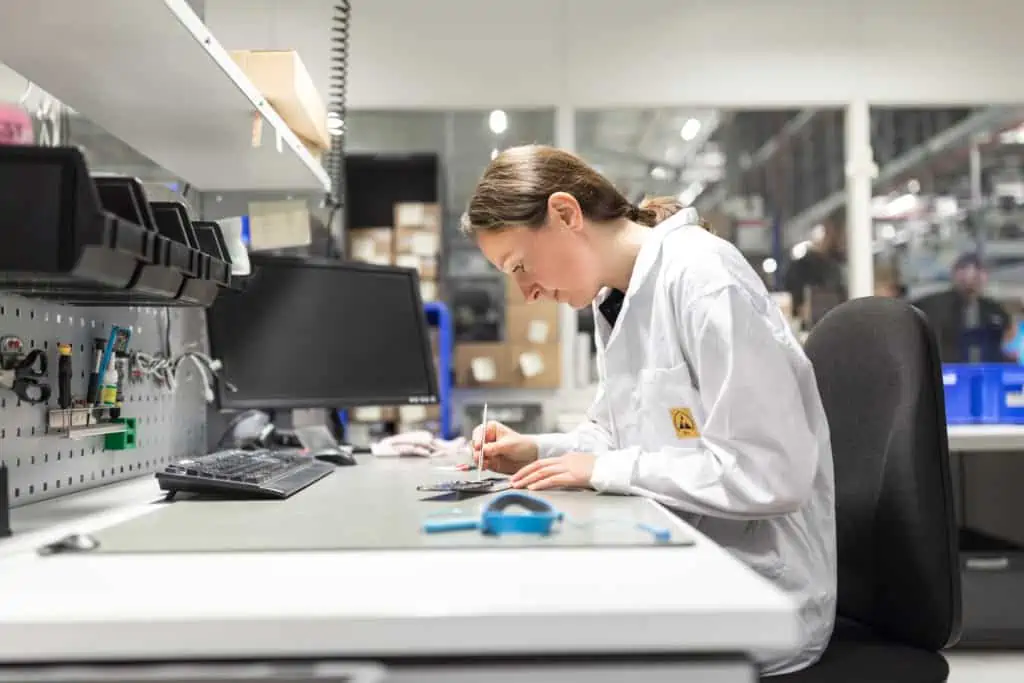
The coronavirus pandemic has made it painfully clear how a society can be forced to adapt to a new situation with virtually no advance warning. It also stands for the many other crises which could emerge in the future and affect not just the economy. Future generations of company staff, in other words those who are currently still in training and education, must be prepared for coming challenges and tasks. This naturally applies also to students at the Institute of Business Engineering headed by Prof. Waldburger at the University of Applied Sciences of Northwestern Switzerland (FHNW). How can factory planning topics such as process mining or material flow analysis continue to be communicated in an understandable and professional manner?
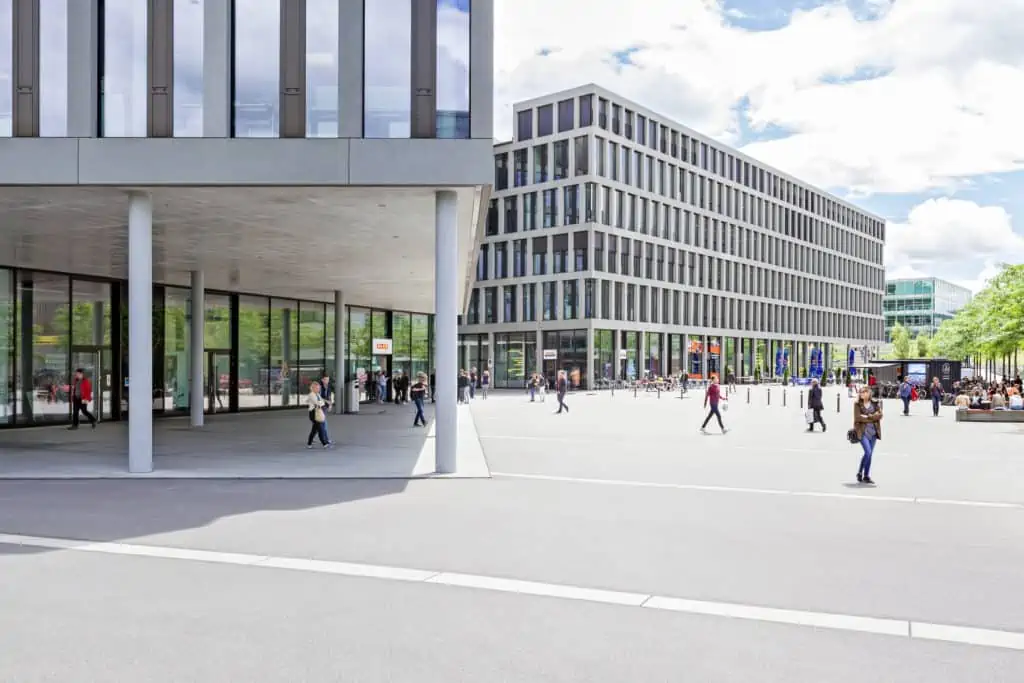
Teaching process mining and material flow analysis via home office
Where students used to spend their day between face-to-face lectures and practical seminars, teaching has had to be converted to a system of online conferences and distance learning. Colleges and universities face new challenges regarding use of the most varied software tools in their practical training. Special applications often run only in computer pools to which access is currently severely restricted or even not possible at all. Within the framework of a practical case study, plavis enabled Prof. Waldburger to offer his students uncomplicated access to the planning software visTABLE®touch on their own computers.
The simple and intuitive handling ensured that no lengthy familiarization was necessary and the students could immediately focus on the task in hand. Another important aspect for Prof. Waldburger:
“visTABLE® is ideally suited for factory planning thanks to the way production process data from the analysis are combined with process mining and layout data.”
In this way, the relationship between product, process and layout can be shown very clearly.
The case study presented the students with a task with a very practical background. The repair station of a smartphone manufacturer was to be moved to a new location in the production center. The process modeled in the ERP system, however, was to remain unchanged. The objective of the move was to optimize the layout such that the transport requirements for intralogistic processes (transport via manual trolleys) are minimized. Naturally there were also other criteria to be taken into account, such as the extent of the available space and the dimensions of the workplaces.
The basic principle of process mining
A very important first step for the students was analysis of the current process by way of process mining. Process mining – Wikipedia
The relevant data are often already available in digital form. By way of process mining, the students learn to acquire these data in their entirety and thus to gather all the information necessary to complete the set task.
This is of very practical use for their future careers, as companies frequently use different software systems for their various data. Furthermore, there are often no direct interfaces and no direct communication between the users of these systems and the data they hold. As here in the case study, where process information could be taken from the ERP system, layout information from the CAD system, and all further information had to be uncovered by the students themselves or else derived from the discussions.
To be able to solve the task, the students had to build a process map with the most important key performance indicators on the basis of the various information sources.
The material flow analysis in visTABLE®touch based on process mining
On the basis of this process map and with the further planning results, it was then possible to design a layout with the planning software visTABLE®touch. Thanks to the straightforward color-coding of different layout objects, it was quickly possible to determine a structure with minimal transport efforts.
Using the various evaluation functions, for example to assess logistics flows or network loads, it was a relatively simple matter for the students to compare and summarize their own results in the context of the objectives to be achieved.
At the end, each student team had the opportunity to present its results in a joint online meeting. According to Prof. Waldburger, the students were especially impressed that:
“… they could even plan in the layout itself and received direct feedback on the impact of their changes.”
Perhaps one or other of these students will one day be responsible for production planning in a pharmaceuticals company and can put this newly acquired knowledge to practical use. And perhaps we will then not have to wait a whole year for a vaccine, but could already be in a position to supply in half this time or even less.
The combination of innovative methods, such as process mining, and innovative tools like visTABLE® can here play an important role in training and education. Practice-oriented knowledge must also be conveyed to future planners and factory operators in difficult times in order to prepare them for the future.