How is optimization potential validated in daily operations?
SFS Group Germany GmbH in Olpe, a small town not far from Cologne, manufactures tailored fastening solutions under the umbrella of the Swiss SFS Group. With turnover totaling CHF 3,090.8 million in 2023 and a workforce of 13,200 employees (FTE), the SFS Group is one of the world’s leading suppliers of application-critical precision components and assemblies, mechanical fastening systems, quality tools and logistics solutions.
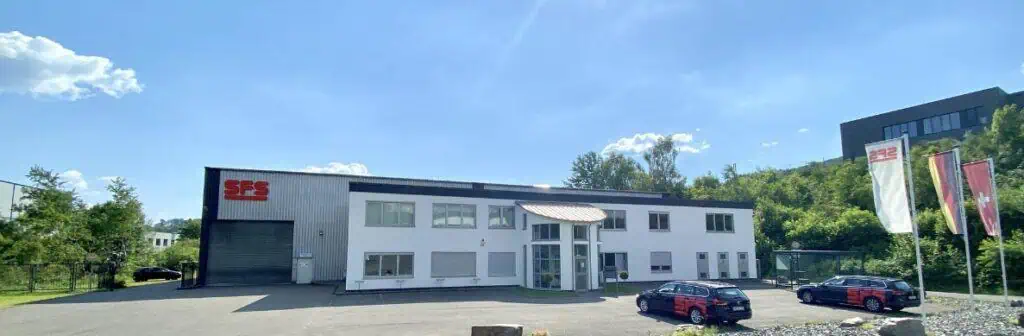
Products bearing the well-known brand names GESIPA®, MBE and SFS are developed and manufactured in Germany. The Olpe location counts approx. 50 employees and has almost 6,100 m² of production space at its disposal.
The company’s cold forming specialists produce a broad spectrum of both traditional and modern fastening elements.
“Distances and the possibilities to optimize routing were the decisive aspects for us,”
Mert Moustafa, project manager – SFS Group Germany GmbH, Olpe
The latest planning project at the site was intended to unlock possible optimization potential, especially with regard to transport processes. Key questions were:
• Is it worth the necessary outlay to swap two areas at opposite ends of the production space that are currently assigned to product shipping and wire storage?
• Is there further untapped potential that still lies dormant in the manufacturing processes?
For Mert Moustafa, the wire storage area stood at the center of attention, as this is the starting point for all flows of raw materials used in production. But how could he confirm that his assumptions were correct?
Product families entered step by step with visTABLE®logix
“We had no time to play around with the software. Planning had to be completed in just two months. The recommendation to use visTABLE® came from the colleagues at our Heerbrugg location. Thanks to the excellent support provided by plavis GmbH and the user-friendly design of the software itself, we were able to validate our ideas for optimization,”
Mert Moustafa, project manager – SFS Group Germany GmbH, Olpe
SFS entered its various articles and processes into visTABLE®logix step by step. This proved to be quite a challenge, because the operational data was not all available on a per-article basis. In this industry, it has always been usual – and generally also meaningful – to think in terms of mass flow rates, for example in tons per day. Accordingly, it was first necessary to collect data on container sizes and their weight capacities, so as to be able to determine the number of individual transport processes involved and thus the transport costs. This allowed everyone concerned to view the material flows and the associated costs from a completely new perspective.
Software support as an important contact for questions
Even detailed questions relating to calculation of the article quantities per pallet and corresponding container capacities were answered without delay by the visTABLE® support team. The users also felt that it was especially convenient to have fast and simple access to useful documentation in visTABLE®.
As Mert Moustafa recalls: “As soon as we realized that we could simply click on the question mark to jump directly to a relevant help page, we were able to solve most of our questions ourselves. This help function is really super.”
The outcome was the first ever evaluation-ready planning layout for the location. SFS can now evaluate transport distances at the press of a button to determine the transport costs. This possibility to visualize process figures led to some interesting results.
Instincts and feelings vs. hard facts
The optimization potential, which everyone had assumed would be considerable, turned out to be much smaller than expected. The improvement was found to be between 17% and at most 25% in terms of the current work time, which equated to a saving of just EUR 1,000 per year. As far as SFS was concerned, that was not enough to warrant a reorganization of its production, and so the costs for complex restructuring could be saved.
On the other hand, it was revealed that the quality control process, for example, required employees to walk considerable distances, and that this could be avoided with a minor optimization of the layout. The focus was thus shifted to improvements that could be implemented quickly. The team was very impressed with the knowledge gained through the use of visTABLE® in this project:
“The software definitely exceeded our expectations,”
Mert Moustafa, project manager – SFS Group Germany GmbH, Olpe
SFS is now planning to conduct annual review meetings to determine its next steps and to perform any necessary validation, depending on future changes in its product portfolio.
Summary
visTABLE® will continue to be used to optimize production and to confirm potential for improvement at the Olpe location in the future. The analyses will cover the whole production process, from material storage and the departments for forming and additional operations such as drilling and thread-forming, through to the process steps coating, sorting and packing.
We would like to thank SFS Group Germany GmbH in Olpe for the commitment to our fruitful partnership and wish the company continued success in the future!