The Weidmüller Group offers products, solutions and services in the industrial environment of power, signals and data. There are production facilities, sales companies and representa-tives in more than 80 countries.
In fiscal year 2014, Weidmüller generated sales of € 673 million with around 4,800 employees.
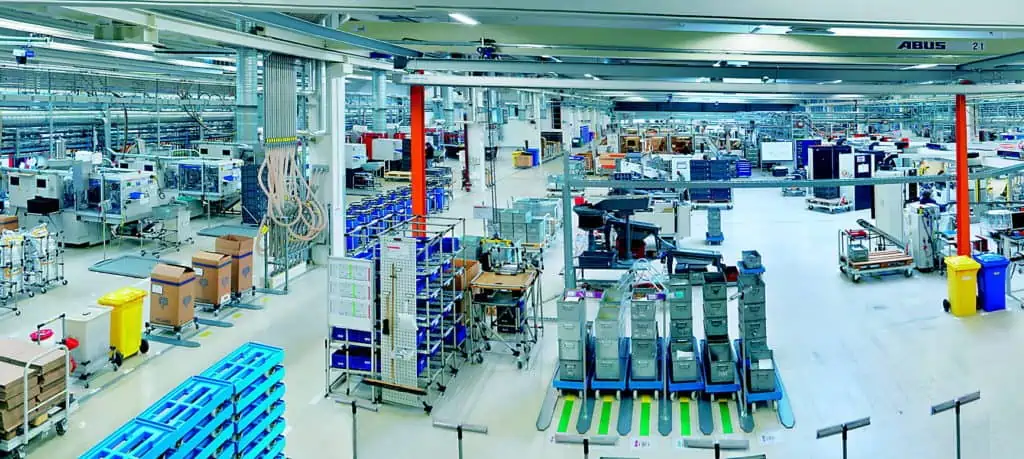
The planning solution of the hidden champions
The standardization of corporate processes often places high demands on larger companies. Weidmüller, as an innovation driver, is also meeting this challenge in factory planning. Until now, the focus in this discipline has been on working with MS Visio. In practice, this enabled simple setups of machines and workstations to be realized in a 2D layout. However, there was a lack of real planning support for decisions on an optimal set-up in the factory of tomorrow. In 2013, the impulse for change came at the congress “Planning + Building Excellent Factories” with visTABLE®.
The first positive impression was the con-vincing visualization in 3D. Furthermore, bottlenecks in the material flow could be made visible at the push of a button and areas could be balanced. I was also con-vinced by the simple operation, which was exactly what we wanted.
– R. Kühnlein, Head of Processes and Network Design
In 2014, Weidmüller seized the opportunity to take stock of a plant in Thu-ringia. The results convinced the company. And so, in 2015, they ultimately decided in favor of visTABLE®.
Effective planning right from the start with visTABLE®
Quickly integrated into the team
By opting for a contemporary planning tool, Weidmüller also reorganized internal processes to get the full potential out of this solution. After only a quarter of a year, the team, consisting of 4-6 employees, had already successfully com-pleted several initial projects with visTABLE®touch. Currently, they are working on the optimization of assembly processes. The recipe at Weidmüller is “from coarse to fine and back again”.
With visTABLE®touch I can intuitively follow this planning approach. I particularly like the area bal-ance and material flow evaluation.
– R. Kühnlein, Head of Processes and Network Design
It started in October 2015 with a 3D visualization of a production area in Detmold with professional mod-eling support from plavis GmbH.
When it comes to joint decisions from intralogistics to the plant manager, visualization is crucial with us. visTABLE® creates acceptance both qualitatively and quantitatively.
– R. Kühnlein, Head of Processes and Network Design
DiThe future in sight
Weidmüller has thus created an ideal combination of qualitative and quantitative layout evaluation for itself. In the future, however, the company has even more plans. For example, upstream processes are now to be adapted and coordinated with visTA-BLE®touch. In Detmold, the pilot area will be used as a starting point for the step-by-step over-planning of the other plant areas.
As soon as we have achieved these goals, we want to tackle our international locations and then, in the long term, also plan new plants consistently with visTABLE®.
– R. Kühnlein, Head of Processes and Network Design