Material flow planning software
- Material flow analysis MFA
- Material flow optimization
- Flow diagram
- State analysis of intralogistics
Material flow is the most important thing in a production company. Because industry products are created from material within processes. Only when these are sold can the factory cover its costs. That is why it is important to move material quickly and directly between the necessary value-added processes (so called flow of material).
visTABLE® software turns this necessity into a creative planning task with the possibilities of the Digital Factory, leading to vivid and comprehensible results. Its visualization and evaluation functions, e.g. as diagram, guide the user specifically through material flow optimization.
Thus, system designs can be evaluated and optimized with their complex system effects at the same moment from different perspectives, which can significantly improve and optimize the management of raw materials, materials and inventories.
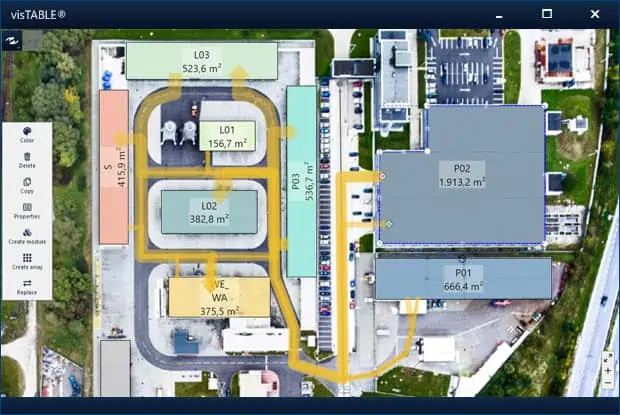