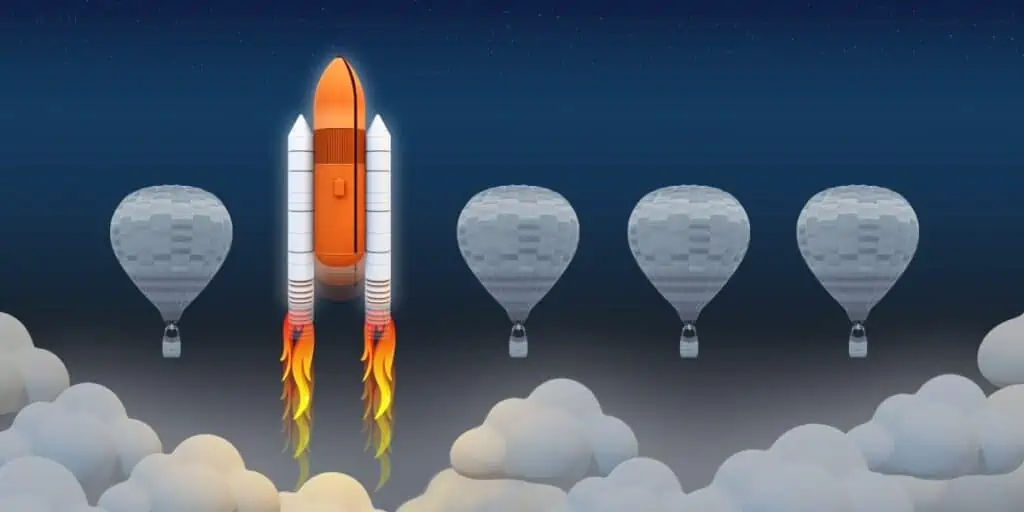
Very many, if not most, planning projects in industry involve restructuring the manufacturing site:
- Part of the manufacturing is to be relocated to another site.
- A product generation is replaced by a new one.
- New series order for the company is in acquisition.
- A turnaround technology promises growth.
So space for manufacturing is needed somewhere, and often there is even space available somewhere else in the facility. If the new asset fits where the old equipment is moving, replacing it quickly appears to be the most practical and cost-effective solution. But in many cases, this does not work out. Then more restructuring has to be done, the reorganization project takes its course …
So many variants!
This immediately raises the question of what all needs to be touched or should be touched. Sometimes, long-held ideas come to the surface.
“If we tackle this now, we might as well tackle that too. We’ve wanted to do that for a long time anyway.”
Thus, the solution space quickly expands to a corporate reorganization. The more is questioned, the more diverse the possibilities become. Orientation becomes increasingly difficult. In addition, different objectives and experiences come together, and everything has to be taken into account. After a short time, hand sketches of the production layout circulate, showing how one or the other could be imagined.
You are well-advised to fix everything at least once to scale. That way, overly fixed ideas are quickly ruled out. And yet, as a rule, a large number of possible variants remain, the elaboration of which consumes countless hours of work. In this case, in particular, valuable time is wasted on dealing with detailed problems in setting up individual plants in the variant X, Y, or Z, while it is not even clear which overriding objectives and key figures must or should be pursued with the restructuring.
Don’t get lost in details
Thus, the proverbial second step is often taken before the first. This is because methodical factory planning gets rid of details when it comes to restructuring. Instead of locating plants and other production equipment directly in a detailed layout, factory planning in this case only looks at the space and room requirements. These are initially put into a structure without detailed consideration of the plant geometries. The resulting rough layout is evaluated and detailed work is only put into preferred variants. This saves time.
Merge Value Stream and manufacturing layout
The Value Streams of the manufacturing provide orientation. They can be described without considering equipment geometries and can be linked to space requirements. Digital factory planning in particular enables very efficient working methods. Our video uses an example to illustrate how this works.
After the reorganization is before the reorganization
Working with digital factory models opens up another advantage if you establish the competence to do so in-house. After all, experience shows that the need for factory planning activities is constantly increasing. Innovation cycles are becoming shorter and production layouts are therefore less stable. Change and transformation in manufacturing are already the order of the day in many companies. Therefore, consider restructuring and layout planning as a continuous task that creates competitive advantages if you can act quickly and reliably. This can be achieved with digital factory models that are capable of linking value stream and layout. After all, an effective layout is based on the optimal value stream. Those manufacturers who master value stream and layout in a digitally integrated way can plan quickly and continuously and secure necessary change on a model basis.
Related topics:
- What you should definitely know about Factory Planning
- How do factory layouts depend on the Value Stream?
- Site development – Relocation of production at DEHN
- 6 principles to help your next planning project succeed
No problem, simply subscribe to our Blog-News!