Most companies, at some point, are faced with the task of expanding or relocation of their plant. Perhaps warehouses or logistics have outgrown their existing space and simply need to move to a new location with more space. Perhaps a site analysis has revealed a need to be closer to key customers or a distribution center. Location decisions may depend on the necessary infrastructure, transport and manufacturing costs, intralogistics and warehouse technology, or other qualitative location factors. But before relocation services even come into play and moving the heavy equipment like industrial racking and machinery, a medium to long-term project plan is needed for successful plant relocation.
Unless you deal with relocation on a daily basis, the process of moving to a new facility can be particularly challenging or even frustrating. A plant relocation is associated with high costs and must therefore be planned properly. Whatever your specific reasons for in-house site planning, the following factors will help solve the site planning task.
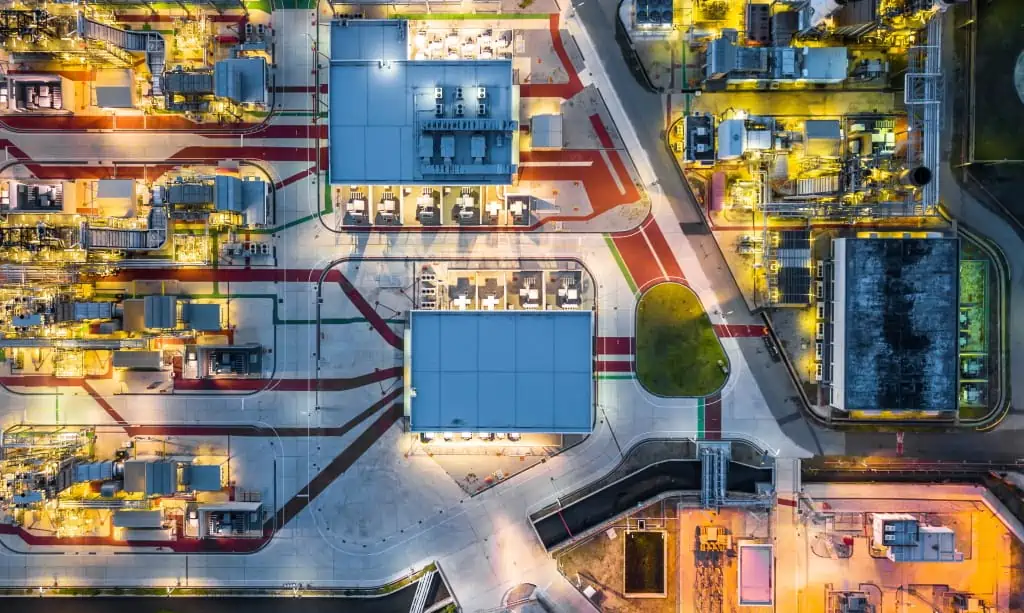
Where does the impetus for choosing and designing the new facility come from?
There are many reasons to change a factory or logistics site. Already knowing the trigger implies ideas and questions for factory layout planning, especially if you are looking for external advice. Which business points does the current location not fulfill, which criteria do you consider necessary? Do impulses come from the customer, from the company management or from the supply chain management? Are you familiar with examples from industry, reference books or universities? Is there already a pre-selection of optimal locations, or do you strive for a selection by calculating location factors and which are these?
What goals does management pursue with relocation to a new site?
Here, factory planners and consultants often speak of a north star to which internal factory planning should be aligned. Give great importance to these overarching goals when evaluating the optimal solution. Only those who have this objective in mind can develop a concept for logistics, warehousing and production, make decisions and evaluate the location factors. Measurable objectives influence solution approaches and results. They should be ambitious, offer opportunities for creativity, be comprehensible to all involved and be verifiable at any time. No two companies are exactly alike; every management pursues different goals. Weight these goals by using KPIs that you can then feed into a cost-utility analysis, for example.
Give structure to your relocation project
Whenever factories, logistics, warehouses and production are to be optimized in an internal site planning project, complex change projects result. To make these plant relocation projects successful, to give the site an optimal layout or to make logistics planning manageable, the project should be structured in phases. One can orient oneself here at general procedure models of factory planning. Many examples can be found at universities and in the literature.
“Just plan a new hall with 7,000 m². When the building is in place, we’ll take care of the necessary production layout.”
No project manager will be satisfied with such an approach. Either the manufacturing hall is oversized and expensive, or the floor plan design does not meet the goals of the plant relocation project. Experience shows that a concept describes 80% of the total life cycle costs of the production facility. Roughly, site planning projects can be divided into the following phases:
- Idea
- Concept
- Planning
- Realization
- Evaluation
Decisions in upstream project planning phases determine the procurement of new automated production facilities and machinery or the selection of a new logistics center. Therefore, these early phases are of great importance before a contractor actually moves the equipment and is starting the installation of industrial racking and heavy machinery in the new plant. No one, not even a consultant, has the possibility to play through all solution variants. Business managers make decisions based on upstream work, their goals, KPIs including costs, and by approval of all stakeholders.
Relocating your manufacturing plant is teamwork
The quality of the solution is very much dependent on the competence and experience of the team members. Only when competencies and experience are lacking should they be acquired outside of one’s own company. In the end, this also affects, among others, contractors who carry out the relocation of all equipment.
Tools tailored for site planning and optimization also help to build competencies and close knowledge gaps. You don’t need an expert in every area right from the start. Ideally, tools help a company’s employees develop into experts as their tasks grow. Also, give your teams the freedom to learn
In smaller teams, discussions about requirements, framework conditions, opportunities, risks, cost, and benefit assessments for warehouses, logistics, and transport costs for the site run more clearly. The conclusion of each phase of internal site planning is the decision, which is made by the team.
Choose an approach that can be implemented by your teams
It is demotivating for team members to work on details while the master plan is not yet in place. Also, it is even more problematic if there is no possibility for the team to get a common picture of this master plan. Match the required accuracy and tolerance of goals, facts, and figures to each phase of the project. There is no one ideal solution for any of the tasks, but a multitude of solution options.
“I’m supposed to plan out the distribution center, but our colleagues in production can’t show us a rough production layout yet.”
Give your team the opportunity to create a common understanding. Often this is a new layout. Sketch, evaluate, compare and select alternatives for further detail. The approach for layout drawings should be from coarse to fine. Your tools should be up to the task and not require highly detailed data at early stages that may not be available at that level of detail at those times. In the concept phase, balancing the workload of production lines to the very least second is not advisable, if the transport effort is still 50% too high elsewhere
Who makes the decisions for the company?
As trivial as it may sound, site planning involves making choices over and over again in each phase. Multiple solution options emerge in each of the phases. From a business perspective, it does not make sense to plan through all options across all project phases of site planning. It must be possible to change decisions made as knowledge and data improve. In complex layout planning, this is perfectly normal and strengthens the project team.
The basis for this is the procedure described above and the use of suitable tools that make this diversity of variants manageable. Involve those affected in these decisions, establish change management. Site planning always leads to change. Change is a management responsibility.
Conclusion
Relocation your manufacturing plant to a new site can be one of the most costly and time-consuming processes because it affects a very large number — if not all — areas of the company. Each department has different concerns, requirements and established workflows that they have perfected over time. Redesigning an optimal site is an opportunity to improve these processes and structures sustainably. Therefore, don’t just put together a ready-made plan in a boardroom and assume it will work. Site planning is one of those tasks where you should work closely with those people on the ground who add value to their production and logistics processes
“There’s only one thing potentially more frustrating than an unstructured relocation to a new facility: having to set everything up a second time in your new site because you hadn’t worked out a solid concept beforehand or hadn’t bothered to communicate with your team about it.”
The success of your site planning are impetus, goal setting, structure, teamwork, approach, decision-making. They make the process controllable and minimize risks.
No problem, simply subscribe to our Blog-News!