Let’s take a closer look at what BIM actually is. Where are the advantages and why BIM will not be suited to substitute factory planning? When using BIM software, it is always decisive for success to create the appropriate understanding amongst those involved. And this not only for the building project itself. It is therefore imperative for the employees to be involved and using a sophisticated strategy. Because BIM also creates extended possibilities in the digital factory and factory structure planning.
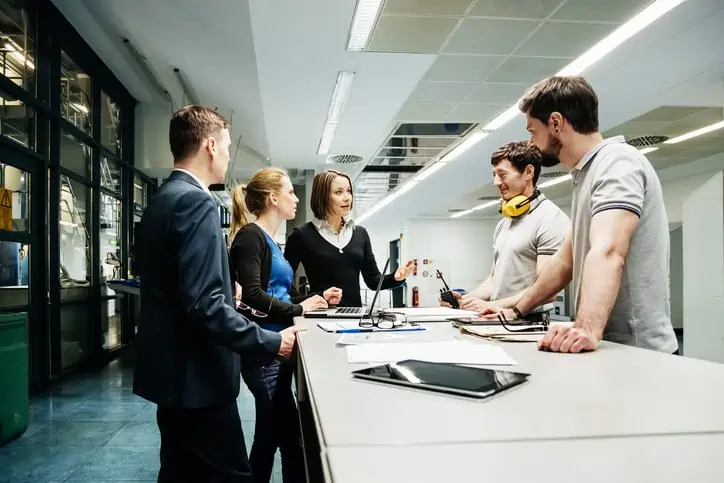
BIM (Building Information Modeling) has been established as a standard in industrial construction. Formal standardization has already been developed successfully all over the world. In Germany, it is implemented by the Association of German Engineers (VDI) “Civil Engineering and Building Services” (VDI 2552 Series of Standards). And it is performed in cooperation with buildingSMART for being international (for example, in the form of the ISO 16739 standard). In other words: The use of BIM software is mandatory to remain competitive.
BIM is basically a procedure and not a technology, at least not primarily. Consequently, BIM methodology cannot become effective solely via software. On the other hand, BIM projects cannot be implemented without digital models, which finally require BIM software in the process. The use of BIM software is thus the only way to create and visualize BIM data and to communicate and cooperate with stakeholders.
First the methodology…
It is not the declared objective of the BIM methodology to perform all these tasks with one single tool. This would be too complex. BIM software applications are focused on the coordinated exchange of data created by the tools of the individual specialist disciplines. The data is provided in a suitable form via a BIM platform, processable for BIM software. Appropriate arrangements are fixed between the individual planning disciplines in the appropriate fields. That’s done by way of a sophisticated BIM workflow. For example by way of the employer’s information requirements (EIR) and information delivery manuals (IDMs), cf. VDI 2552. In addition, the scope of the information to be included in BIM is defined. In most cases, it is then also about the exchange of information itself with appropriate levels of detail (LoD). It is the responsibility of BIM managers that these rules are observed.
… and then the technology and tools
There is a long-established idea that BIM projects will only succeed if solely one single CAD software is used. However, Building Information Modelling cannot be implemented if those involved are forced to use one specific CAD software. Even though Revit, Allplan or Autodesk Inventor are the most frequently used CAD programs. So what should you do when integrating other specialist disciplines? At the latest when they do not contribute to the 3D building model, open standards and cloud-based BIM technologies are required. AVA software or monitoring of the progress in construction on mobile devices are only two fields of application in the life cycle of a BIM model. Here, BIM authoring programs based on CAD systems just for 3D modeling are obviously less useful.
Only BIM solutions implementing standards according to OPEN BIM will be expedient and have a promising future. The IFC format implemented in the ISO 16739 standard raised international acceptance. IFC files are supported by standard BIM tools. The exchange of native and proprietary data is no longer necessary. This also eliminates the requirement that all stakeholders must use the same BIM software.
IFC (Industry Foundation Classes) provide planners from different fields with appropriate means for the well-structured exchange of information. They can use it to complete their specific information about the field and compare it with other stakeholders. Thus, plausibility can already be checked in the design phase. The IFC standard, pushed primarily by BuildingSmart, allows planners in the individual fields to create information in their specific environment. This is then made available to other persons involved in a well-structured manner from their software via an IFC interface
Benefit even beyond the phase of new planning
Building Information Modelling goes even beyond the stage of design and development of a building. BIM planning also constitutes the digital basis for the realization and accounting of construction services. Consequently, the facility management can access the digital data in a well-structured manner using the information provided by BIM. Thus, BIM implementation covers the whole life cycle of a building.
Advantages of Building Information Modelling used in a factory planning project:
- Structured workflow
- Enhanced communication
- Excellent cooperation using up-to-date digital data
- Production system planners can cooperate with specialist planners of other disciplines of Architecture, Engineering and Construction (AEC) industry
Examples within the framework of factory planning projects
Requirements with regard to building service installations, in particular to media connections, can be specified and documented when planning the logistics system. The reverse case is probably possible in the case of brownfield projects. The factory or layout planner can also access that part of a BIM model. It provides him with information regarding exhaust air, compressed air or pipelines and shafts. This must be taken into account when restructuring the system.
Information regarding the structural calculations of a production building is essential to be able to plan heavy installations in the layout. Floor loads, the influence on vibrations, or restrictions with reference to the vibration and sound absorption can thus already be taken into account at the early stages of the project. Whereas specific CAD software of the appropriate discipline is not required by the building planning engineer, the relevant data must always be provided.
The data collected by way of Building Information Modeling can also be used by other building disciplines. This also applies to other phases of the life cycle of a building. The logistics planner need not necessarily use Revit or Allplan, for example. But moreover the focus for him is on the tasks of planning and design of the program of logistic services and its optimal implementation. This happens primarily with the tools and methods suited for this complex of tasks.
The data collected by way of Building Information Modelling can also be used by other building disciplines. This also applies to other phases of the life cycle of a building. The logistics planner need not necessarily use Revit or Allplan, for example. But moreover, the focus for him is on the tasks of planning and design of the program of logistic services and its optimal implementation. This happens primarily with the tools and methods suited for this complex of tasks.
Limits of BIM in the context of factory planning
BIM software (e.g. Revit from Autodesk) is focused on the building, not production. But a factory does not only consist of buildings. It is rather a means to an end: Industrial construction provides the shell for the production system or imposes restrictions to be considered when planning the production system. Even though this field also includes various partial tasks and disciplines, such as:
- production and assembly planning, manufacturing design
- intralogistics planning
- planning and operation of automation
- materials handling
- storage technology
No corresponding applications can be found in BIM software. In addition: The use of CAD especially for 3D modeling is simply not expedient to solve certain partial tasks.
Factory planning: Fields of planning and partial tasks
To cut a long story short: Factory planning must be examined holistically in coordination and execution of all necessary tasks, without binding all involved to a single software. The software supports the planner in the appropriate specialist discipline, and data helps the plant operator to run the factory.
And there is another aspect that is often neglected. Any brownfield project usually contains little or even no BIM data, at least this is the status as of today. It has not yet been possible to coordinate the requirements of the stakeholders with reference to the BIM process. This also means that cloud solutions can only partially cover data exchange and archiving (e.g. BIM 360).
Conclusion
The BIM procedure is not limited to creation of a digital building model by way of software. It supports cooperation of all specialist disciplines of AEC industry. Any errors in the planning can thus be identified early, rendering the planning more efficiently and minimizing the costs.
However, factory planning is more than that. Also, a BIM system, even if featured with extended functions, only contributes a small part to the overall BIM system. But this does not speak against the use of BIM in industrial construction. Existing Building Information Modeling data can be used in an effective manner when planning the production system with open standards (IFC) where possible. Software for layout planning and factory design should at least provide an IFC interface for import. Conversely, the demands placed on industrial construction are defined when planning the production system. Therefore, they are not to be planned in BIM software
Related topics:
- What you should definitely know about Factory Planning
- CAD models for factory planning – How does it work properly?
- Designing virtual factory halls in system construction
No problem, simply subscribe to our Blog-News!